Oil condition monitoring helps ensure the smooth running of expensive engines and other power systems.
Intertek Oil Condition Monitoring (OCM) tests lubricants for the critical properties needed to reduce the risk of costly engine damage, downtime, and shutdowns.
Key lubricant properties tested and monitored include viscosity, insolubles, flashpoint, water content, acid number, wear metals, PQ index, particle count and base number.
Lubricant quality scanning tests:
Viscosity testing for lubricants:
Using the correct oil with the right viscosity is critically important for good machine operation, ensuring the mechanical operation of systems and components remain within the intended design scope. Used lubricating oils may show an increase of viscosity due to oxidation and nitration, or as a result of contamination with un-burnt fuel components within diesel engine oil. Oil condition monitoring monitors for any unexpected variation. It is beneficial to check that the lubricant-grade in use is what has been recommended by the lubricant supplier.
Insolubles testing:
Lubricants are subjected to environmental stress which leads to contaminants production and inclusion. Contamination degrades base oil and additive systems, producing insoluble particulates which cause serious problems. Contaminants include heat, entrained air, incompatible gases, moisture, internal and externally generated contaminants, partially burned fuel compounds, other oils etc. Regular monitoring for the presence of insolubles in lubricants is useful for large engines, providing an effective tool to help safeguard against costly engine breakdowns.
Flashpoint testing for lubricants:
Flashpoint is the lowest temperature at which a vapour produced by the liquid will ignite when a flame is applied under standard conditions. Below a certain value there is a high risk of very serious incidents in service, including crankcase explosions. Because of the low flashpoint of most fuels, a sudden drop in flash temperature within crankcase oil can usually be relied upon as an indication of dilution. Lubricant flashpoint must be monitored carefully.
Water Content:
Water contamination occurs from various sources in new or used oils. Storage tanks encourage water condensation from ambient air changes, resulting in free water which collects at the bottom of storage tanks over many years. Failure to remove this water will lead to water being drawn into the engine lubricating operational system with potentially catastrophic results. Water is the most common contaminant present within lubricant oil samples. This can cause machine failure due to rust corrosion, bacterial growth, sludge formation and the formation of unstable emulsions.
Acid Number:
Acid Number measures the level of acidity within the lubricant. An increase in the Total Acid Number (TAN) often suggests oxidation of the lubricant, depletion of the anti-oxidants and contamination with acidic components which can cause reduction of machinery reliability due to the build-up of lacquers and corrosive materials.
Wear Metal Elements:
LQS testing reports the levels in of wear metals likely to be found within marine lubrication and engine systems. Increases in certain elements such as Iron (Fe) and Copper (Cu) are early warning signs of a potentially unacceptable wear metal problem. A secondary ferrography analysis can give a detailed analysis, providing the morphology of particles and the number present, an experienced analysis will indicate if a failure is in progress. Learn more about wear metals testing.
PQ Index:
The Particle Quantifier index test (PQ) technique measures the effect of magnetic debris such as iron and nickel on a known magnetic field. The degree of effect is proportional to the degree of ferrous material present. The PQ Index test offers a proactive approach to controlling contamination. In combination with spectrographic metals analysis, PQ index significantly enhance analysts advisory capabilities.
Particle Count in lubricants:
Particle count tests count the number of particles present greater than a given size per unit of fluid. Test results reflect the contaminants present within that size range and are applied to assess fluid cleanliness and filter efficiency. The particle count method is suggested for systems which rely upon cleanliness to protect highly machined and close fitting components from abrasion and detriment caused by the presence of unwanted particulates.
Base Number:
Lubricating oils clean and provide protection from acid and chemical corrosion. The Base Number represents the potential to neutralize acidic properties. Low sulphur fuels mean engines work at higher temperatures with longer oil change intervals, resulting in higher levels of oxidation and organic acids. Sulphur is oxidised which in part combines with water, forming sulphurous and sulphuric acids which are extremely corrosive to the engine’s components and need neutralizing.
Lubricant oil condition quality testing:
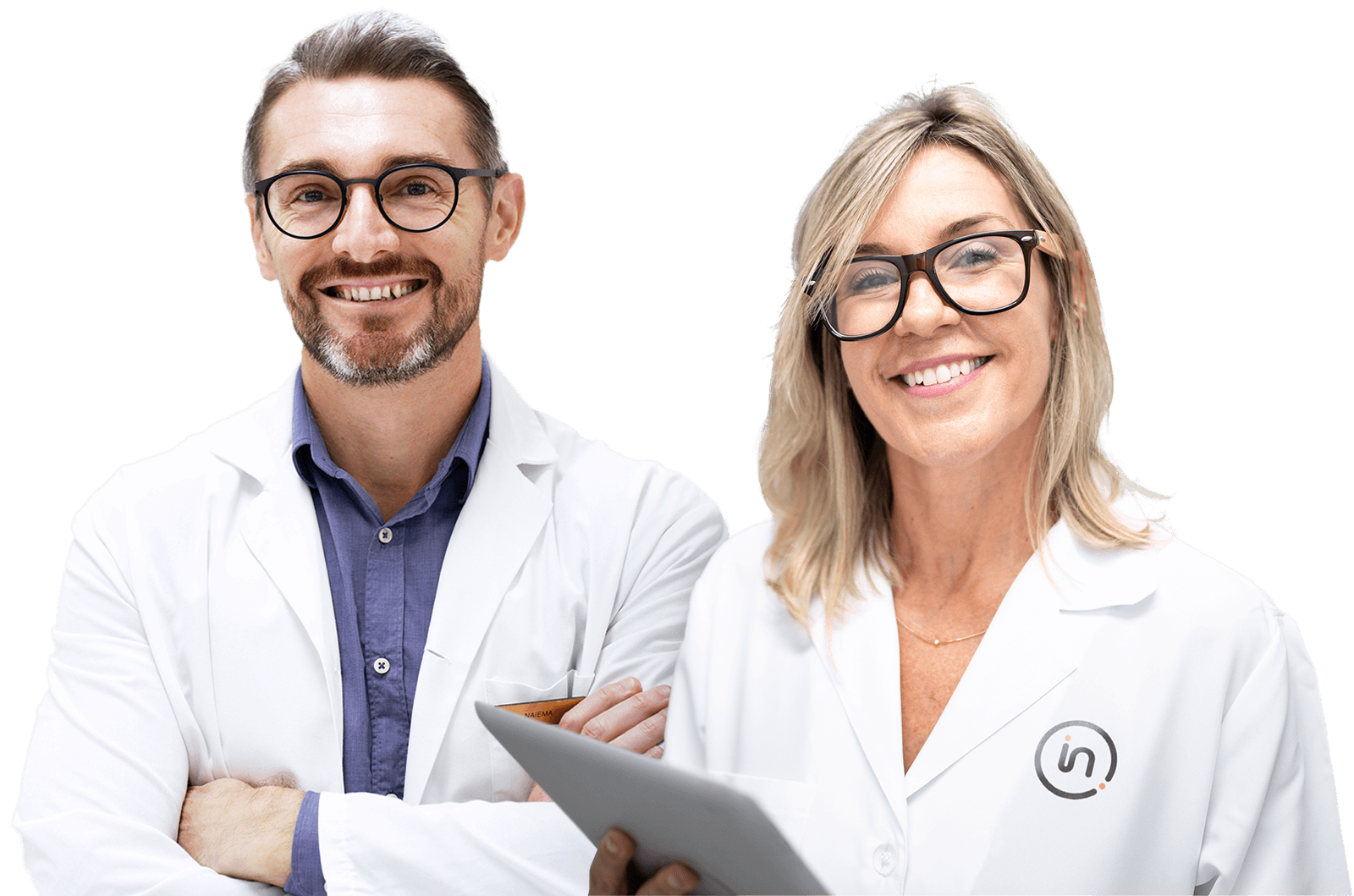