Peel testing expertise for adhesives, coatings and laminates allowing accurate measurement of peel strength, coating durability and adhesive performance
Peel testing allows accurate measurement of the performance of seals, coatings and adhesives and gives invaluable information to resolve failure investigations for adhesives failure and optimize processing parameters.
Seals, laminates and adhesives have been designed to perform many functions. Some applications allow easy to peel flexible layers of seals, such as re-sealable food packaging, whilst others are designed not to remain bonded, such as in automotive or building applications. It is important to understand product performance and processing parameters, such as adhesive application and curing, through accurate peel testing in order to ensure the product is safe to use and performs to expected specifications, whilst preserving your brand image.
Purpose-designed fixed-arm peel instrumentation allows Intertek to accurately measure adhesive toughness as a function of position throughout a delamination process which allows assessment of its strength, evenness and effectiveness. By making careful corrections for both elastic and plastic deformations that occur during the process, it is possible to calculate the intrinsic material parameter correctly. In particular we routinely conduct the T-peel test (ASTM D1876) which evaluates the force required to the progressively separate two bonded, flexible adherends.
Additional tests performed at some of our sites include ASTM D3167, ASTM D3330 Method A (180° peel) and ASTM D3330 Method F (90° peel).
Our mechanical peel measurements are routinely used, in conjunction with microscopy (to examine surface morphology) and surface analysis techniques (to determine surface chemistry), in order to compile a complete picture of the behavior of an adhesive bond, coating or laminate structure.
Our materials scientists conduct peel testing along with a suite of physical and mechanical testing to generate accurate data that delivers the insight you need to develop and test new adhesives, coatings and polymer laminates for wide range of applications such as labels, packaging, automotive, medical devices and construction.
With our expertise we can help you to understand your product’s adhesive physical and mechanical properties and help you to optimize your product performance and processing parameters throughout your product’s lifecycle whilst aiding you in the reduction of direct costs associated with wastage from seal or adhesive failure.
Related Services:
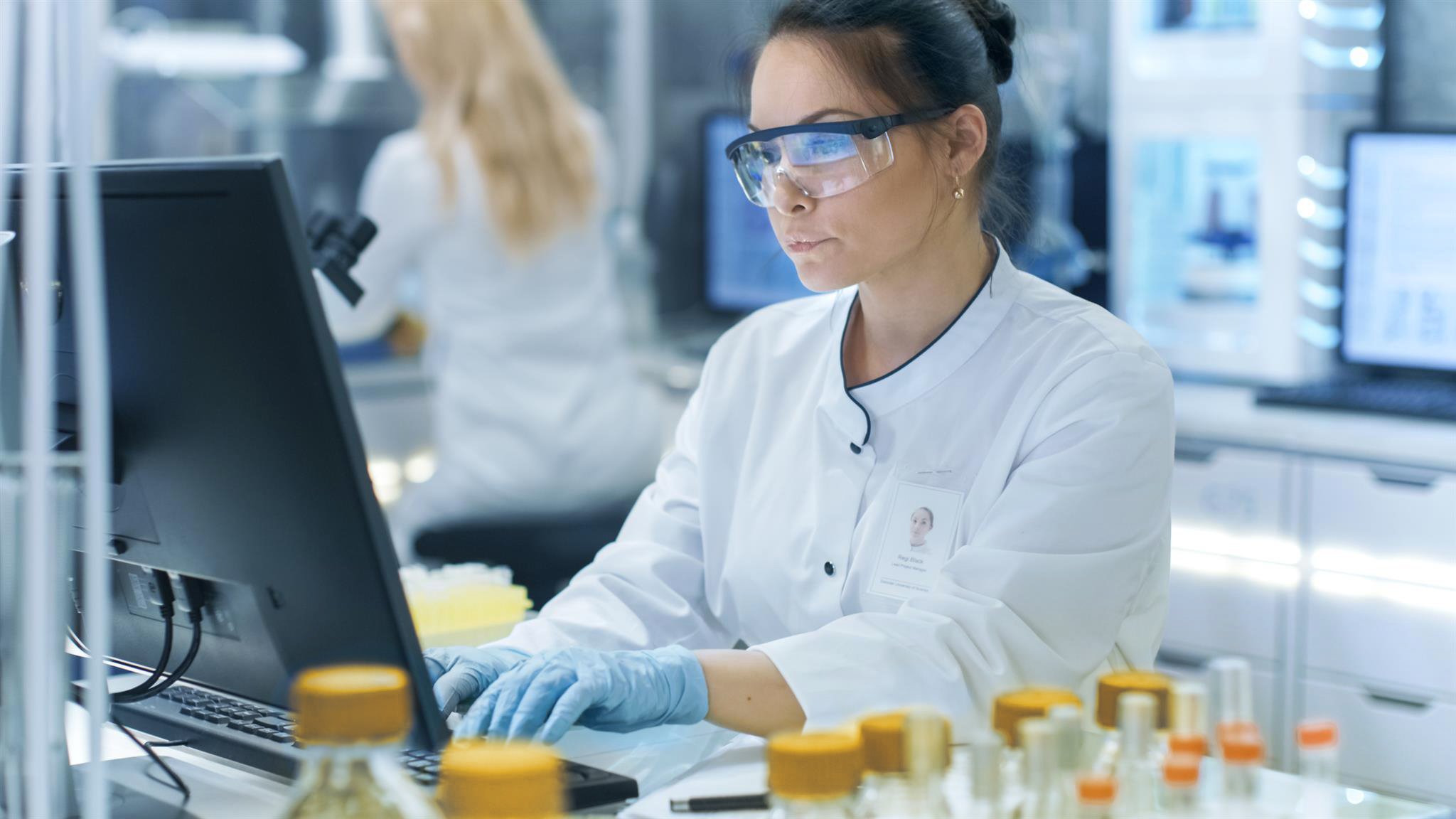
Regulatory Chemical & Materials Analysis Expertise
WHITE PAPERS
WEBINARS
- PFAS Monitoring in Environmental and Polymer Samples
- Microplastics and Nanoparticles - Definitions And Regulatory Considerations
CASE STUDIES
- Dissolution of Hydroxyapatite Coatings for Medical Devices
- Particulate Contamination control and analysis
- Case Study and Fact Sheet: XRF Analysis and XRF2 Mapping
BROCHURES
Intertek Wilton: The Wilton Centre, Redcar, TS10 4RF, UK
Download Directions
Tensile Testing for Plastics
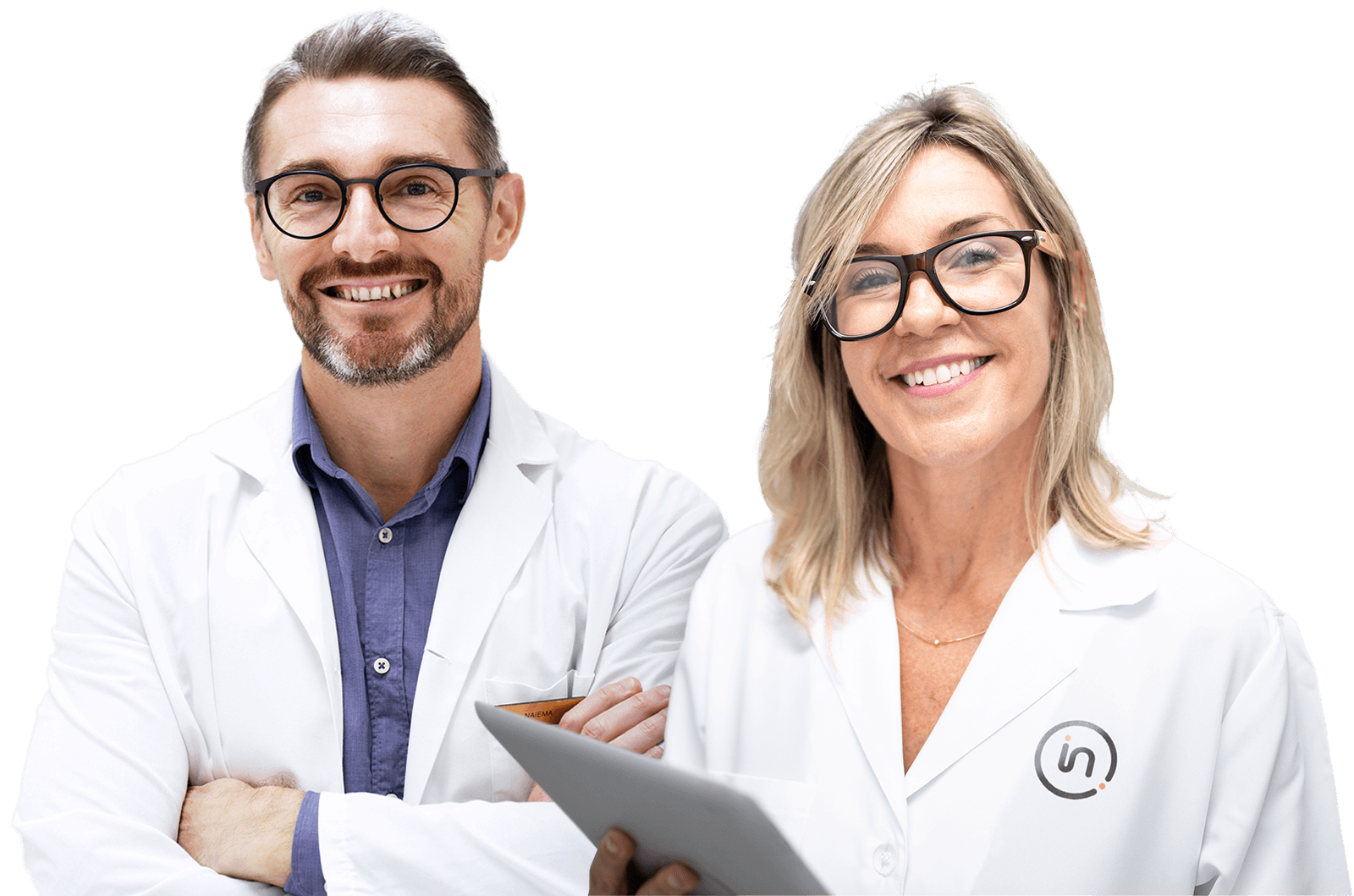