Understanding the total lifetime cost of a product
Consumers increasing favor brands that offer durable, long life products over cheaper, ‘throwaway’ alternatives. This can be both for environmental and economic reasons.
Likewise, corporations and governmental procurement agencies are increasingly focused on achieving lowest lifetime cost (including the cost of business interruption to replace worn out products) rather than lowest unit price. Often, this is not achieved by purchasing the cheapest unit price product.
The LCC process can used on any product category subject intensive, wearing use, from uniforms in fast food restaurants, to power tools used on construction sites.
Intertek’s process can help both either purchaser of the manufacturer:
- Determining the underlying durability factors: Intertek Performance works with your engineering and marketing teams to understand the product’s real world usage, and the most common causes of product failure.
- Developing in-depth test plan: Having understood how consumers really use your product, Intertek Performance develops a test plan that evaluates the product’s performance to failure in the key characteristics that matter most.
- Testing competitors: Intertek Performance tests your product, and those of competitors, to the test protocol(s). This independent test data is fed into Intertek’s proprietary LCC model.
- Results and lowest life cycle cost: Intertek’s LCC model determines the product that offers the best overall value for money. Depending on where the product is used, overall life cycle cost can be significantly affected by incidental costs such as replacement logistics cost and administration cost.
- As a purchaser, these results help you chose the product that will over the life of the contract, offer the lowest total life cycle cost.
- As a manufacturer or brand, these results can help you promote your product to the end consumer, or to support a pitch to a corporate, or governmental, client.
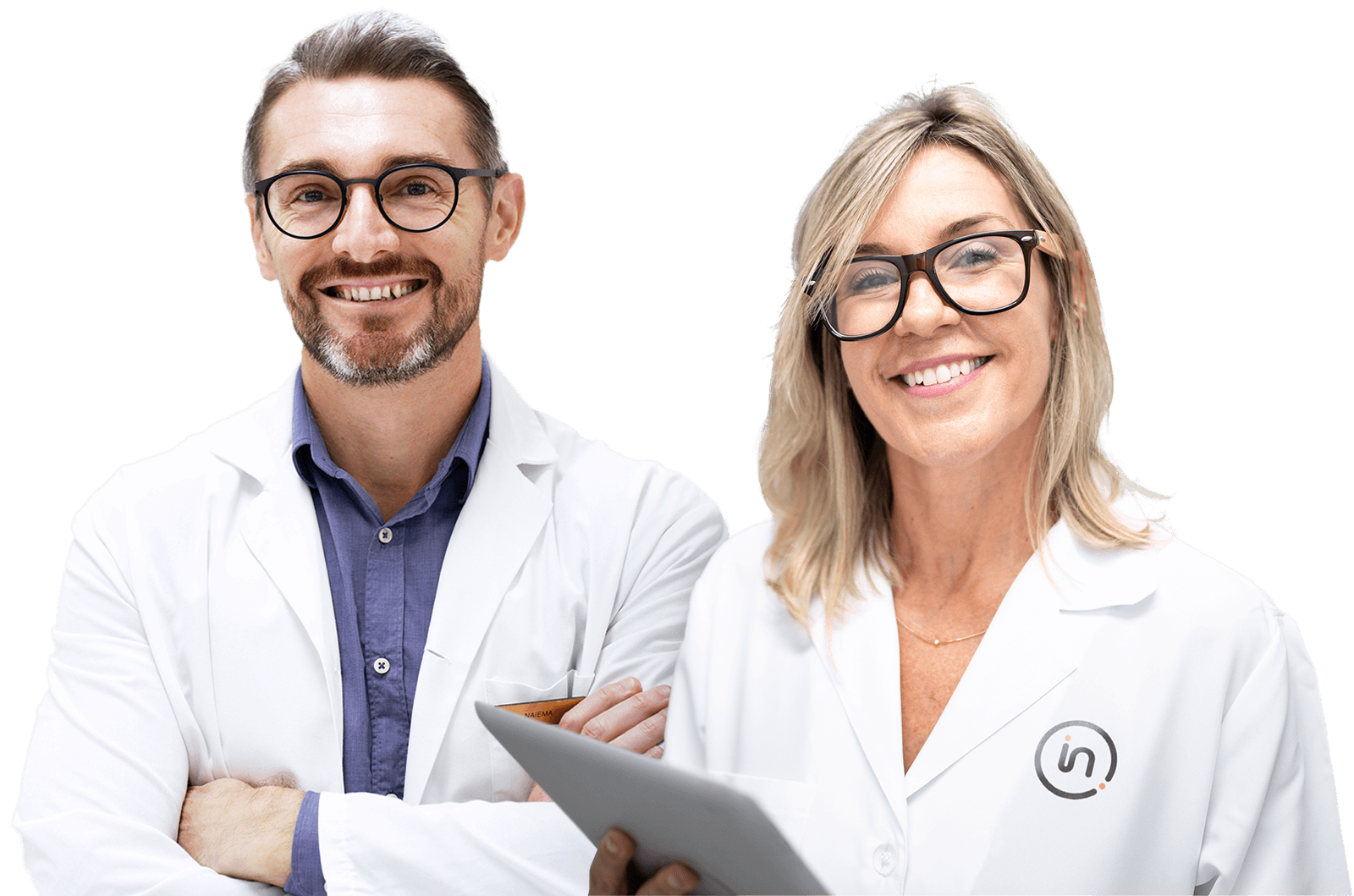