Comprehensive Thermal Shock testing solutions helping you to market fast and efficiently
What is Thermal Shock?
Thermal shock occurs when a material is exposed to a sudden and significant change in temperature, causing rapid expansion or contraction in different parts of the material. This abrupt temperature change can lead to stress within the material, potentially causing cracks, warping, or even failure. Some common factors that can influence thermal shock are: thermal conductivity, thermal expansion coefficient, material strength and toughness, and temperature gradient.
What is Thermal Shock Testing?
Thermal shock testing simulates a products life cycle by exposing the product to rapid changes of temperatures ranging from -60°C to 170°C. This is completed by using a dual climate chamber that will transfer the product from one temperature extreme to the other, in less than 30 seconds. The number of cycles, soak times and temperature extremes are determined by the nature of the products intended use. These parameters can be defined by the customer or determined by an associated test specification.
If you require Intertek to conduct a thermal profile development to determine saturation times of your product, Intertek’s engineers are well versed in this process.
Thermal Shock Testing Specifications: MIL STD 810, Method 503; USCAR-2 Section 5.6.1; DC-10611 Section 6.1.5; CS 00056 Section 5.3.5; GMW 3172 Section 9.4.2
Key Benefits of Thermal Shock Testing
Thermal shock testing is a critical tool for ensuring safety, performance, and customer satisfaction in temperature-sensitive applications. Some of the key benefits include:
- Improved Durability and Reliability
- Identifies materials or products susceptible to failure under rapid temperature changes
- Ensures that components can withstand the stresses of real-world operating conditions, enhancing their lifespan and performance
- Early Failure Detection
- Reveals potential weak points, defects, or vulnerabilities in materials or designs, such as microcracks or weld weaknesses, that might not appear under normal testing conditions
- Enhanced Product Quality
- Encourages the use of materials and designs that can handle extreme thermal conditions, leading to higher-quality products
- Prevents premature failures, reducing warranty claims and maintenance costs
- Validation of Design and Manufacturing Processes
- Confirms that manufacturing techniques, material choices, and design tolerances meet performance requirements
- Helps in validating compliance with industry standards and customer specifications
- Safety Assurance
- Ensures that products exposed to thermal shock remain safe and functional, reducing risks to users
- Cost Savings in the Long Run
- Mitigates the risk of catastrophic failures during operation, avoiding costly repairs, replacements, or liability issues
- Reduces the need for extensive field testing by simulating extreme conditions in a controlled environment
- Regulatory and Certification Compliance
- Meets industry-specific testing standards (e.g., MIL-STD, USCAR, etc.), which are often required for market approval
- Optimized Material Selection
- Provides insights into which materials perform best under thermal stress, aiding in material selection for new designs or upgrades
- Customer Confidence
- Demonstrates commitment to quality and reliability, enhancing customer trust in the product and brand
What Products Benefit from Thermal Shock Testing?
Thermal shock testing is an essential tool in the automotive industry for evaluating the reliability and durability of products. Download your free copy of our FAQ today.
Intertek's Thermal Shock Testing Equipment:
- Thermal shock chambers with basket sizes from 15” wide x 15” deep to 29” wide x 24” deep
- Walk-in thermal shock chamber with a basket size of 48” wide x 68” deep x 64” height
Intertek's unique walk-in thermal shock chamber with a basket sized at 5.5’ in length, 3.9’ wide and 5.3’ in height is perfect for your large format thermal shock needs. From Automotive glass, HVAC modules and battery modules this chamber is sized for your needs. Shelving can be added or removed to meet your product dimensions. This chamber has a temperature range from 100°C to -50°C and will transition in less than 30 seconds from one temperature extreme to the other.
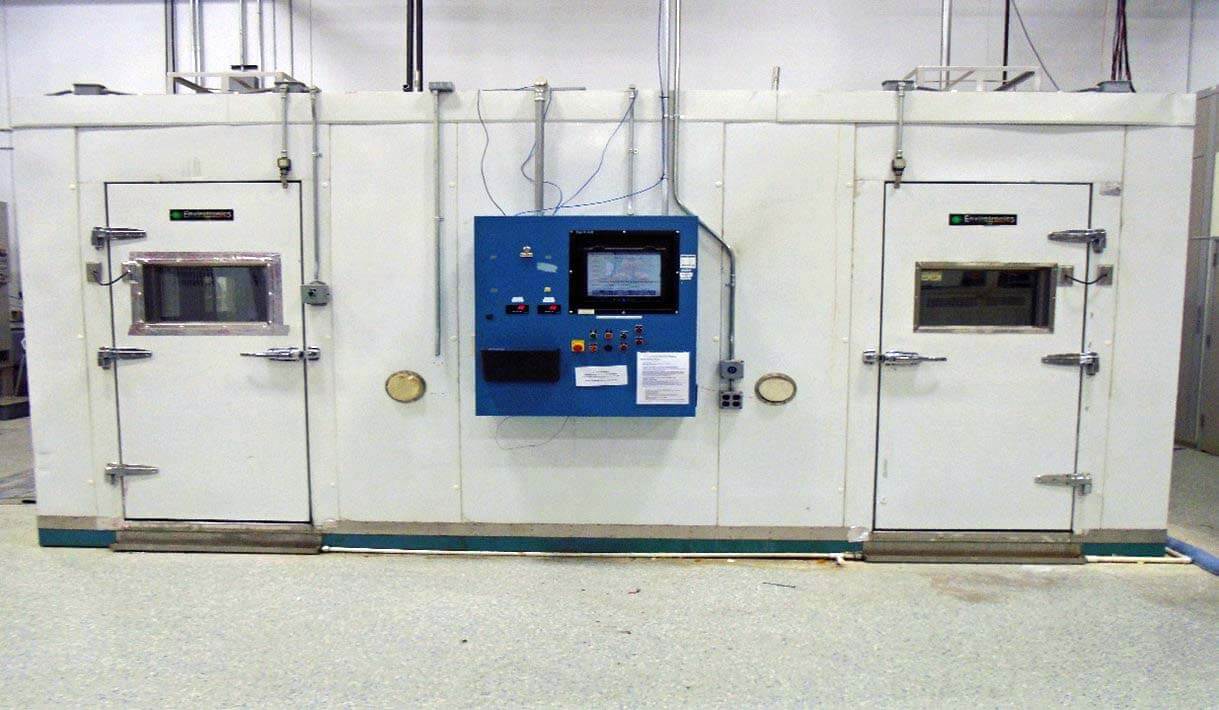
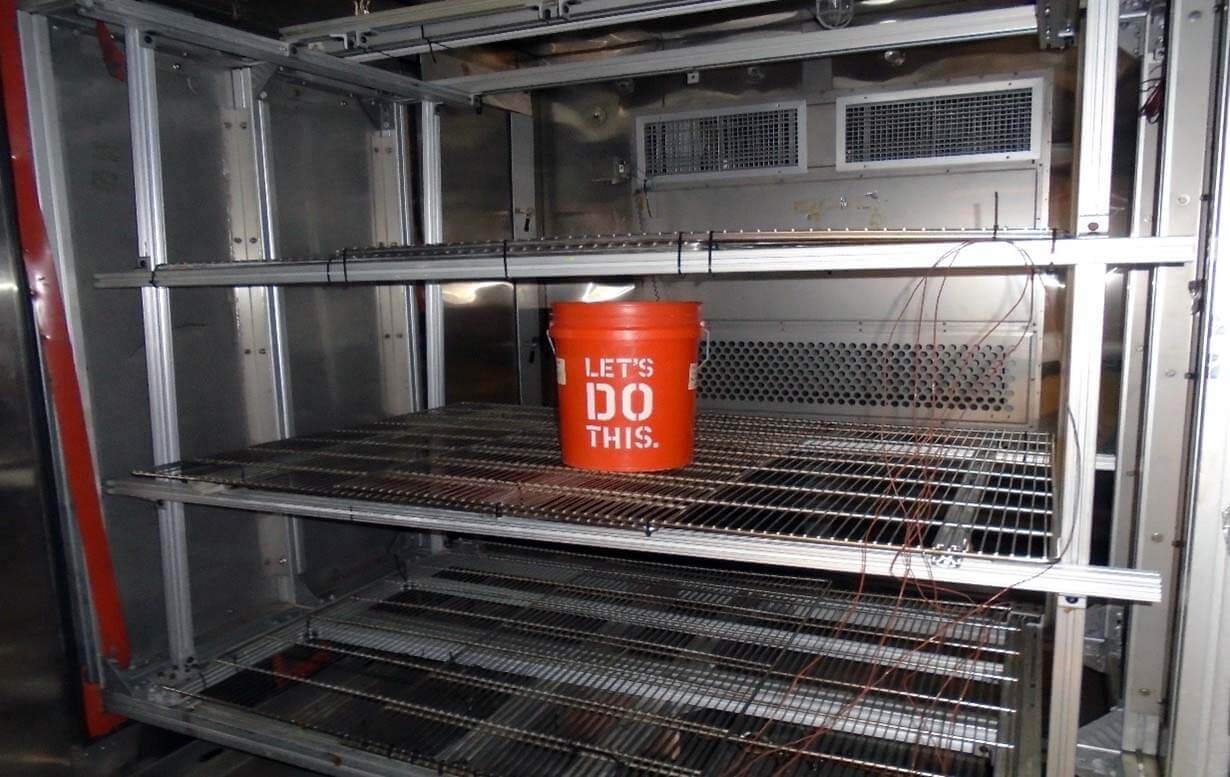
Intertek has a variety of chamber sizes to meet your needs. Introducing Intertek’s new Tri-Chamber which allows for more shelf space resulting in increased capacity, great for mid-sized products.
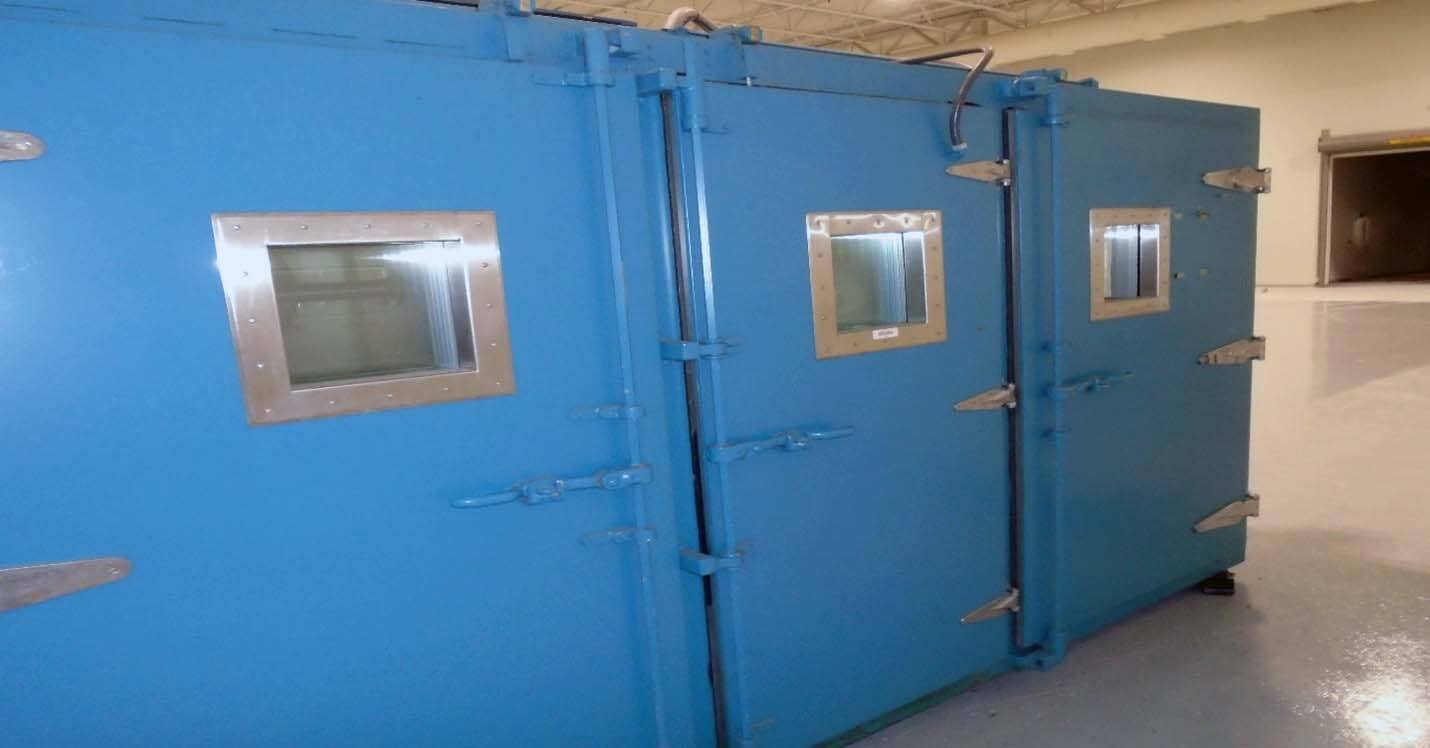
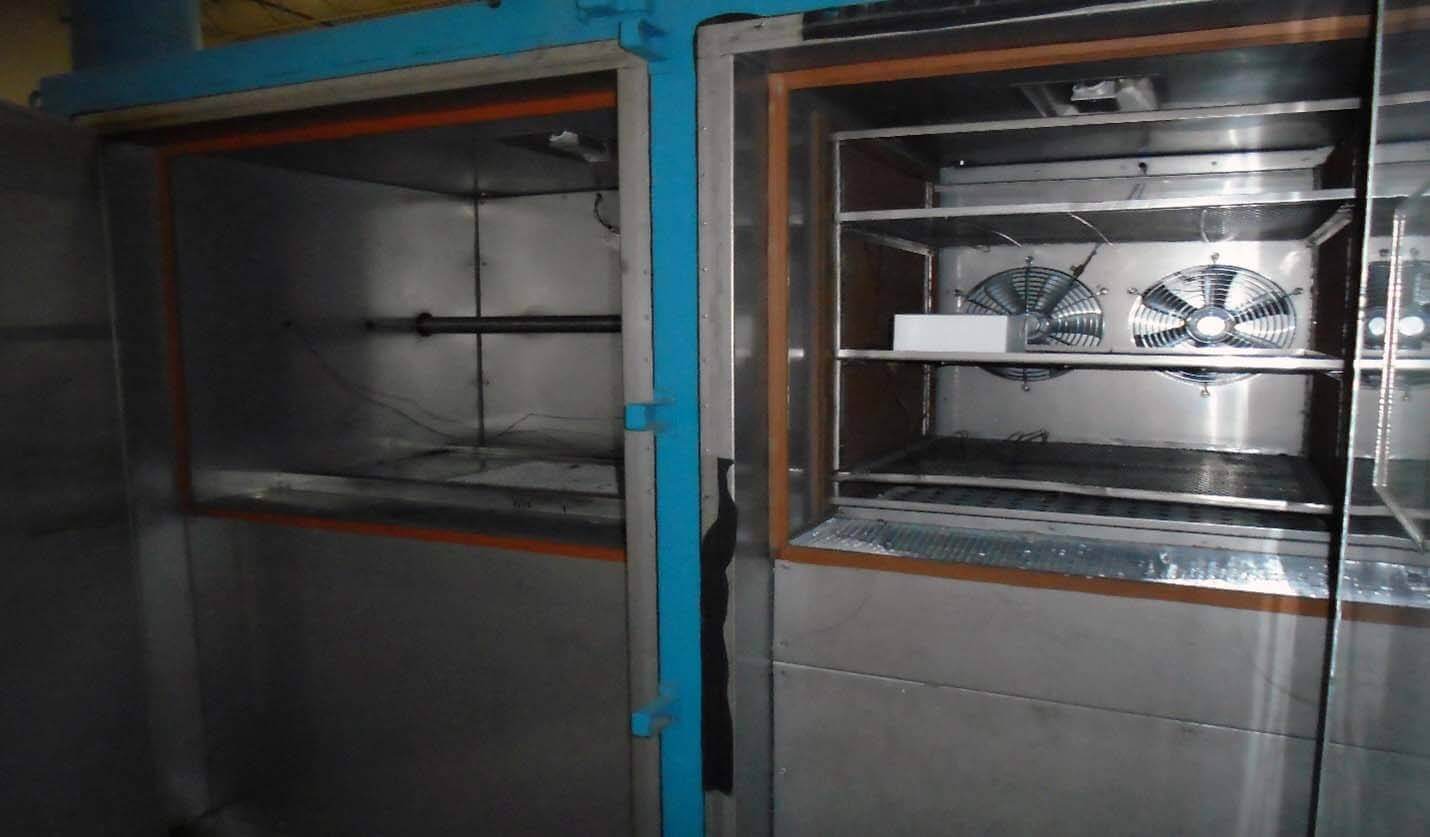
Additional Thermal Shock Testing Chambers
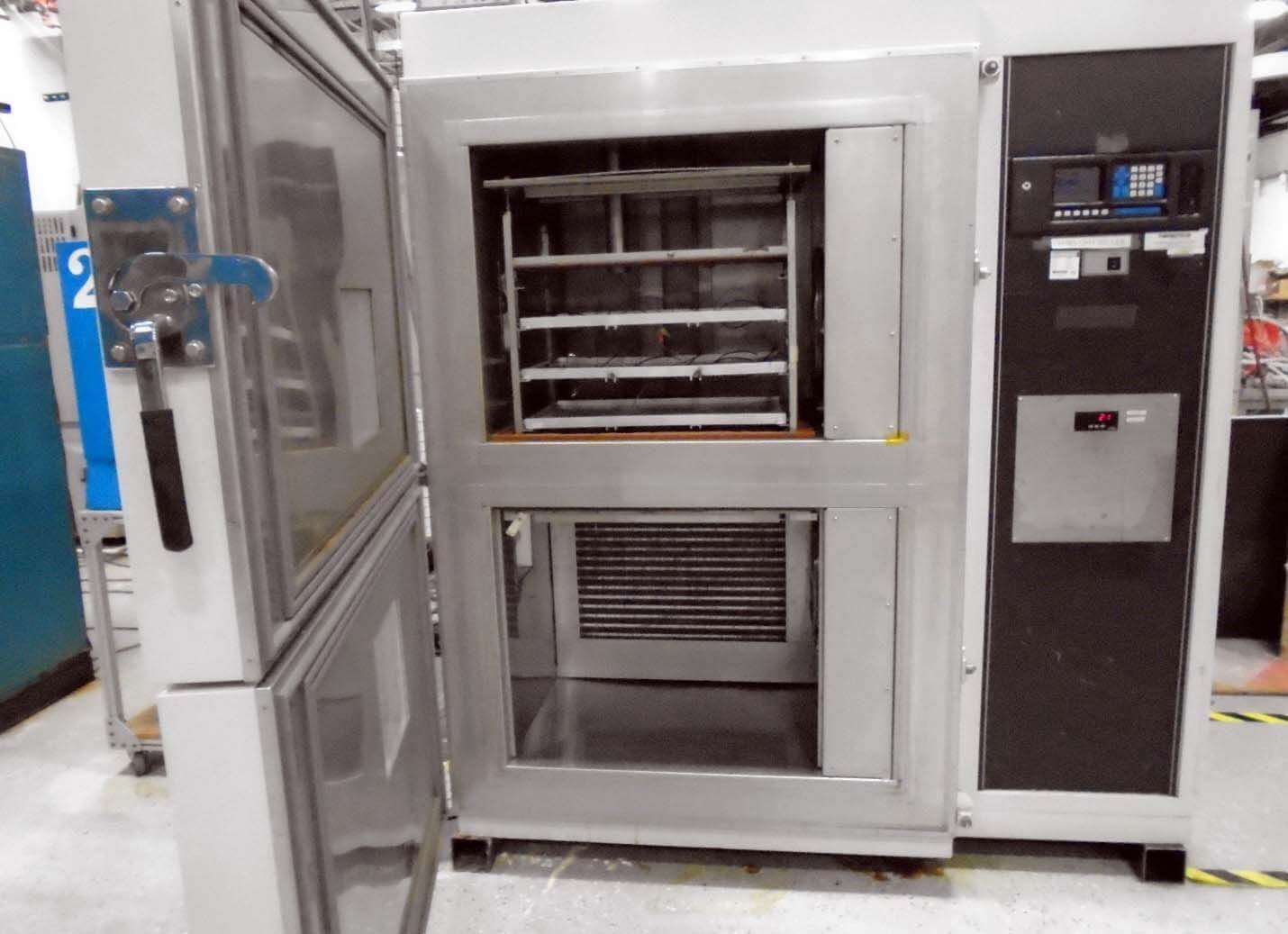
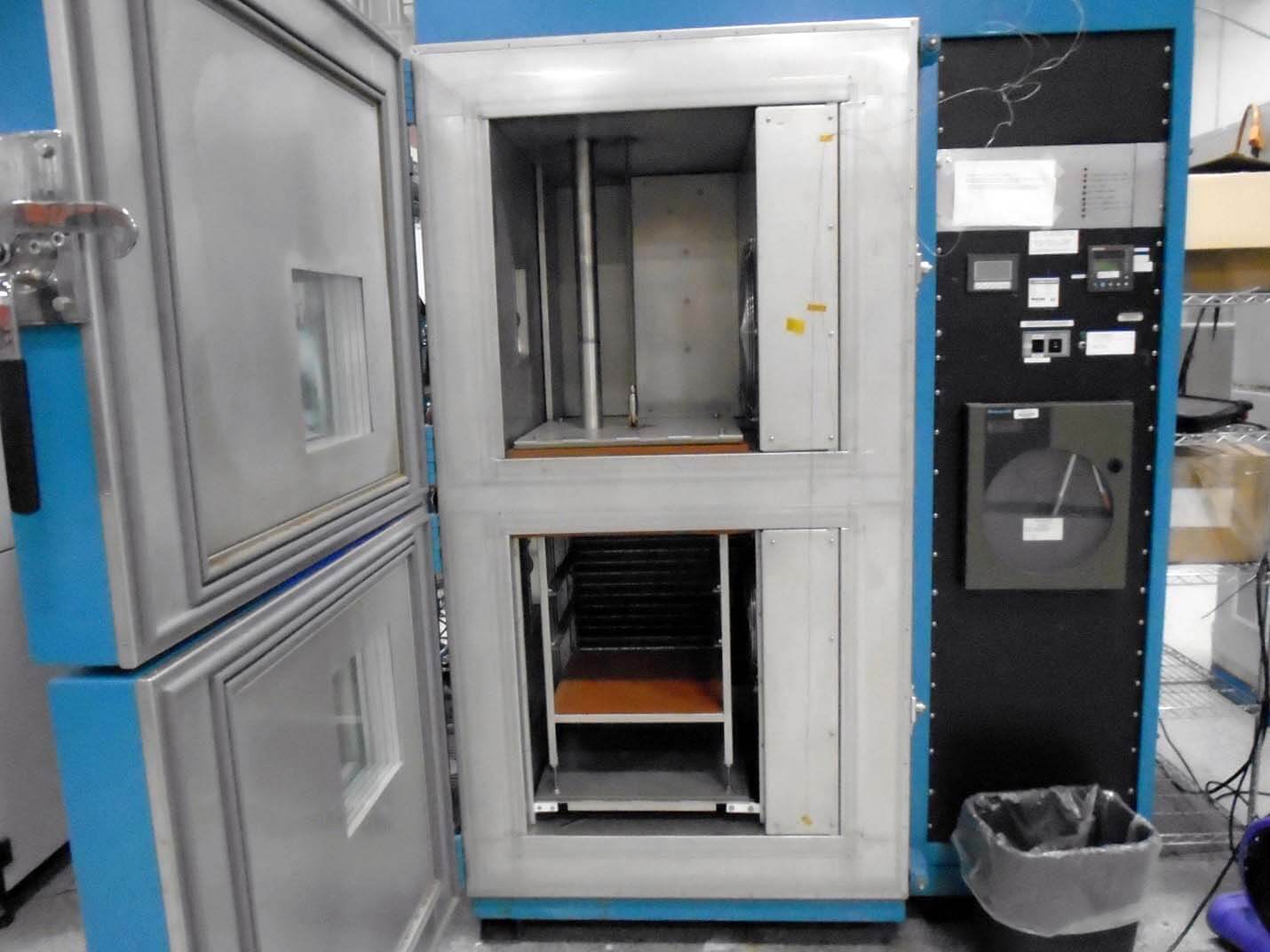
Knowledge Center
Master FMVSS 108 Compliance – Download the Expert Guide
Automotive Functional Safety & Cyber Security FAQs
Development of Driveline Electrification Technologies White Paper
Understanding Failure Analysis and Answering your Frequently Asked Questions
The Top-7 FAQs of Autonomous Vehicles Testing
The Top-10 FAQs of Advanced Composites Testing
The Top-10 FAQs of Automotive Interior Testing
Accelerated Stress Testing to Manage Disruptive Market Changes Webinar
Transitioning to Structural Composites to Meet CAFE Standards
Automotive Interiors Testing White Paper
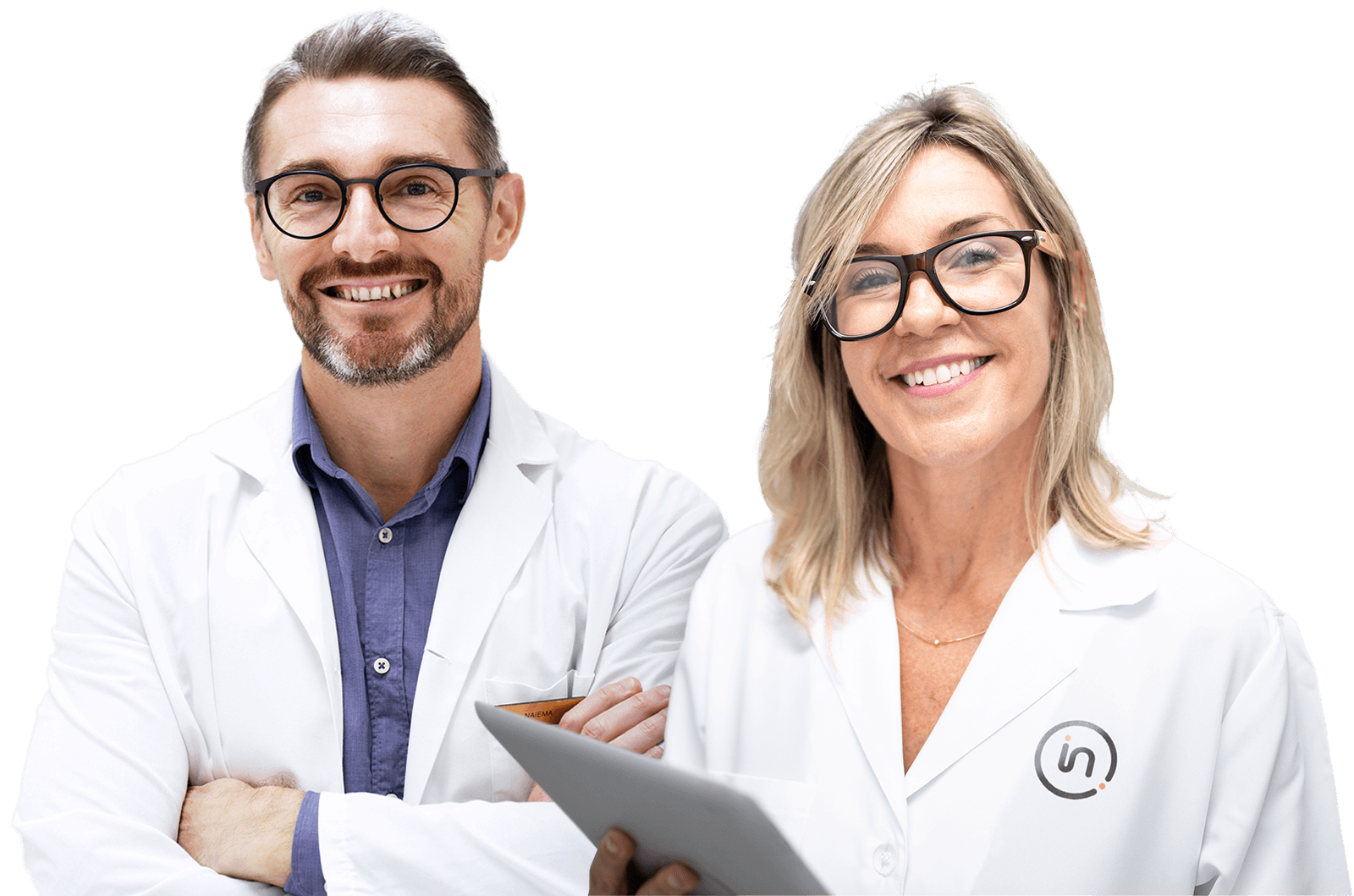