Lighting the Way: A Practical Guide to FMVSS 108 Compliance for Automotive Engineers
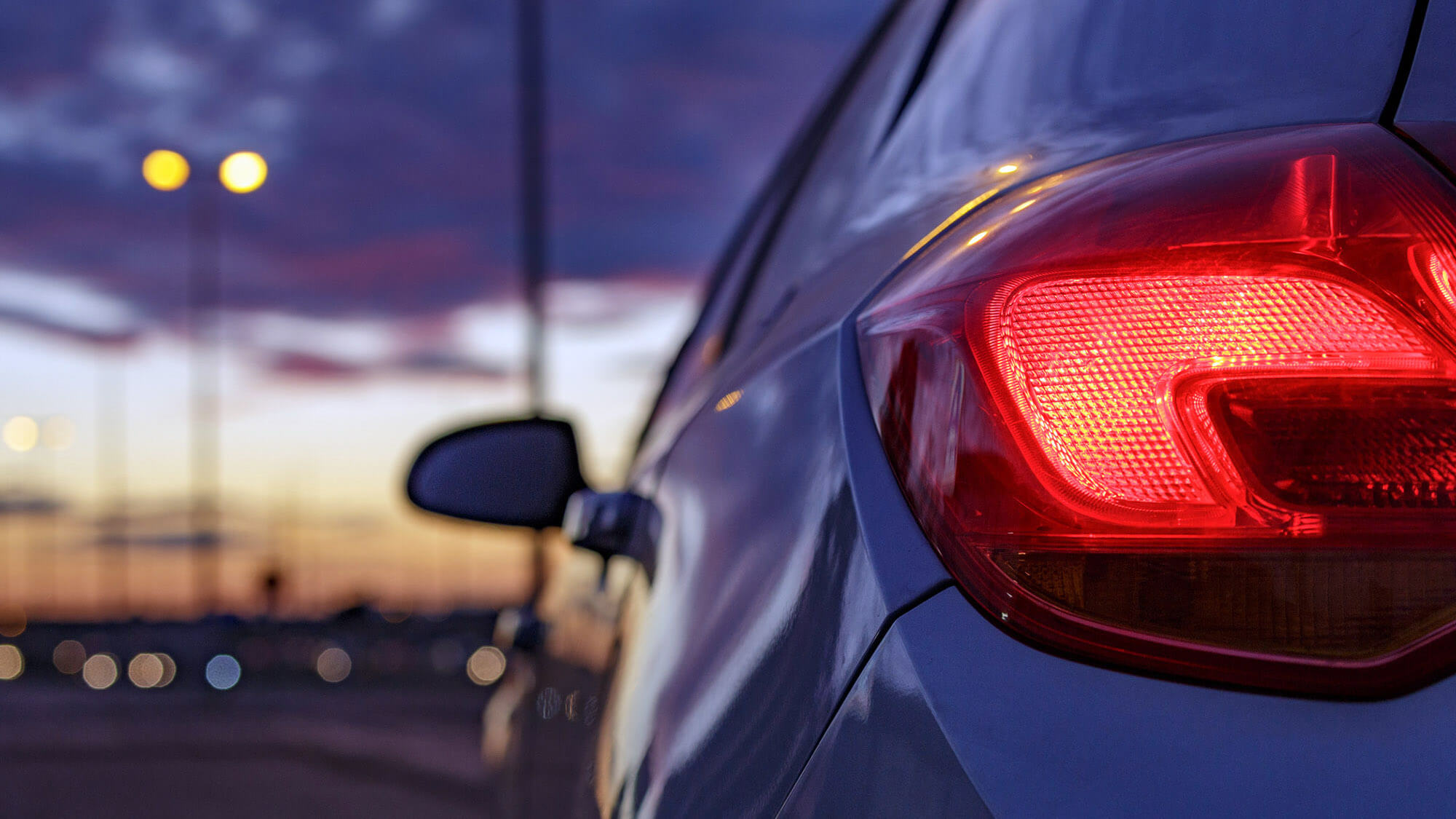
21 Mar 2025
What Engineers Need to Know About Testing, Certification, and Avoiding Common Compliance Pitfalls
If you're designing, manufacturing, or testing vehicle lighting systems, FMVSS 108 compliance is a hurdle you can’t ignore. Whether it’s turn signals, headlights, or reflex reflectors, every automotive lighting component must meet strict federal requirements before hitting the road. But navigating these regulations can be challenging. Let’s break down what engineers need to know about FMVSS 108 and how to ensure compliance without unnecessary delays.
Understanding FMVSS 108: The Basics
The United States Federal Motor Vehicle Safety Standard 108 (FMVSS 108) sets the minimum performance, durability, and photometric requirements for all lamps, reflective devices, and associated equipment used in passenger and commercial vehicles. Administered by the National Highway Traffic Safety Administration (NHTSA), it governs everything from the brightness of brake lights to the beam patterns of headlights.
Compliance with FMVSS 108 isn’t just about ticking regulatory boxes; it directly impacts road safety and liability. Engineers need to consider not only the design of their lighting systems, but also the environmental conditions and real-world performance of their products.
Three Core Categories of FMVSS 108
FMVSS 108 is categorized into three primary lighting system types, each with specific requirements:
- Signal Lamps – This includes turn signals, brake lights, and parking lamps. Each function has distinct photometric and color requirements, ensuring that drivers can accurately interpret visual cues.
- Headlighting Systems – These range from sealed beam headlights to modern LED and high-tech Adaptive Driving Beam (ADB) systems. Beyond basic brightness and coverage, headlights must meet stringent photometric, aiming, and durability standards.
- Retroreflective Devices – These include reflex reflectors and conspicuity systems for heavy-duty vehicles. These devices must be designed to reflect light effectively, even in low-visibility conditions.
Key Performance and Compliance Tests
Each of these lighting systems must undergo extensive testing to validate that it meets the minimum FMVSS 108 standards. Some of the most critical tests include:
- Photometry Testing – Measures the intensity and distribution of emitted or reflected light using a goniophotometer.
- Color Testing – Ensures that lights emit the correct color wavelengths, tested with a colorimeter or spectrometer.
- Durability Testing – Includes vibration, dust, moisture, and corrosion resistance tests to confirm that lamps can withstand real-world conditions.
- Plastic and Optical Materials Testing – Evaluates lens materials for resistance to heat, UV exposure, and long-term weathering.
- Aiming and Alignment Testing – Particularly crucial for headlight systems, ensuring proper alignment and beam cutoff to prevent glare.
For engineers designing adaptive systems, the new ADB requirements introduce additional real-world dynamic testing. This evaluates how the lighting system responds to oncoming traffic and adjusts beam intensity in real-time.
Who’s Responsible for Compliance?
FMVSS 108 compliance ultimately falls on the auto manufacturer, but testing responsibilities are often shared across multiple stakeholders. For example, the lamp manufacturer typically must certify that their product meets regulatory standards before selling it to OEMs or distributors. However, vehicle manufacturers and installers also have obligations, particularly concerning proper lamp placement, activation, and spacing on the vehicle.
To demonstrate compliance, manufacturers need to provide reasonable care documentation. This typically includes test results, quality control processes, and proof that production units meet the same standard as tested samples.
Common Pitfalls and How to Avoid Them
There are a few areas that lamp manufacturers need to be aware of that could pose issues during a production run. These include:
- Inconsistent Test Sample Performance – If early test units pass but production models vary, compliance can be challenged. A robust QC process is essential.
- Misalignment Issues – Headlights that fail aiming tests often need design adjustments or better mounting solutions.
- Environmental Failures – Lamps that pass photometric tests in a lab may still fail dust, moisture, or vibration tests in real-world conditions. Engineers should factor in rugged durability early in the design process.
The Role of Third-Party Testing
Because compliance is both technical and regulatory, many manufacturers outsource to third-party test labs, such as Intertek, for independent validation. Third-party testing offers:
- Accredited Facilities – Equipped with precise testing instruments that meet NHTSA standards.
- Expertise in Compliance – Ensuring that tests are performed correctly, and results are defensible.
- Faster Market Readiness – Reducing delays from failed tests or incomplete documentation.
For manufacturers developing new lighting technologies—such as adaptive LED arrays, laser headlights, or high-performance daytime running lights—working with an external test lab early in the development process can prevent costly redesigns and certification headaches later.
FMVSS 108 compliance is a technical challenge, but it’s one that engineers can tackle effectively with the right testing strategy and understanding of the regulations. Whether designing a simple tail lamp or an advanced headlight system, ensuring compliance from the start will streamline certification and keep vehicles safer on the road.
For those looking to gain a strategic advantage in the market, Intertek experts have put together a valuable resource, the “Lamp Manufacturers Guide to FMVSS 108.” By using Intertek’s expertise in automotive lighting regulations, you’ll have the insights needed to navigate compliance efficiently and accelerate time to market.