The metallurgical laboratory solved a magnet de-bonding issue.
Investigating component failure is an example of the metallurgy testing and consultancy Total Quality Assurance expertise offered by Intertek.
The client asked Intertek to investigate a failed rotor assembly that failed due to de-bonding of two of the magnets from the internal magnet array.
Visual low power microscope analysis clearly showed limited surface coverage of the adhesive in the failed rotor, and the shape of the adhesive was unfavourable. The rotor contained a large central defect, which can promote debonding by mechanisms such as stress raising and/or environmental factors i.e. liquid penetration. The colour of the adhesives also varied.
The failed rotor adhesive was yellow in comparison to green of the good sample. This indicated either a difference in composition of the adhesives and/or environmental degradation had occurred. Optical microscopy showed that the porosity was greatest and significantly thicker in one layer in the failed rotor. Additionally surface defects were also observed on the magnet.
Metallurgy testing:
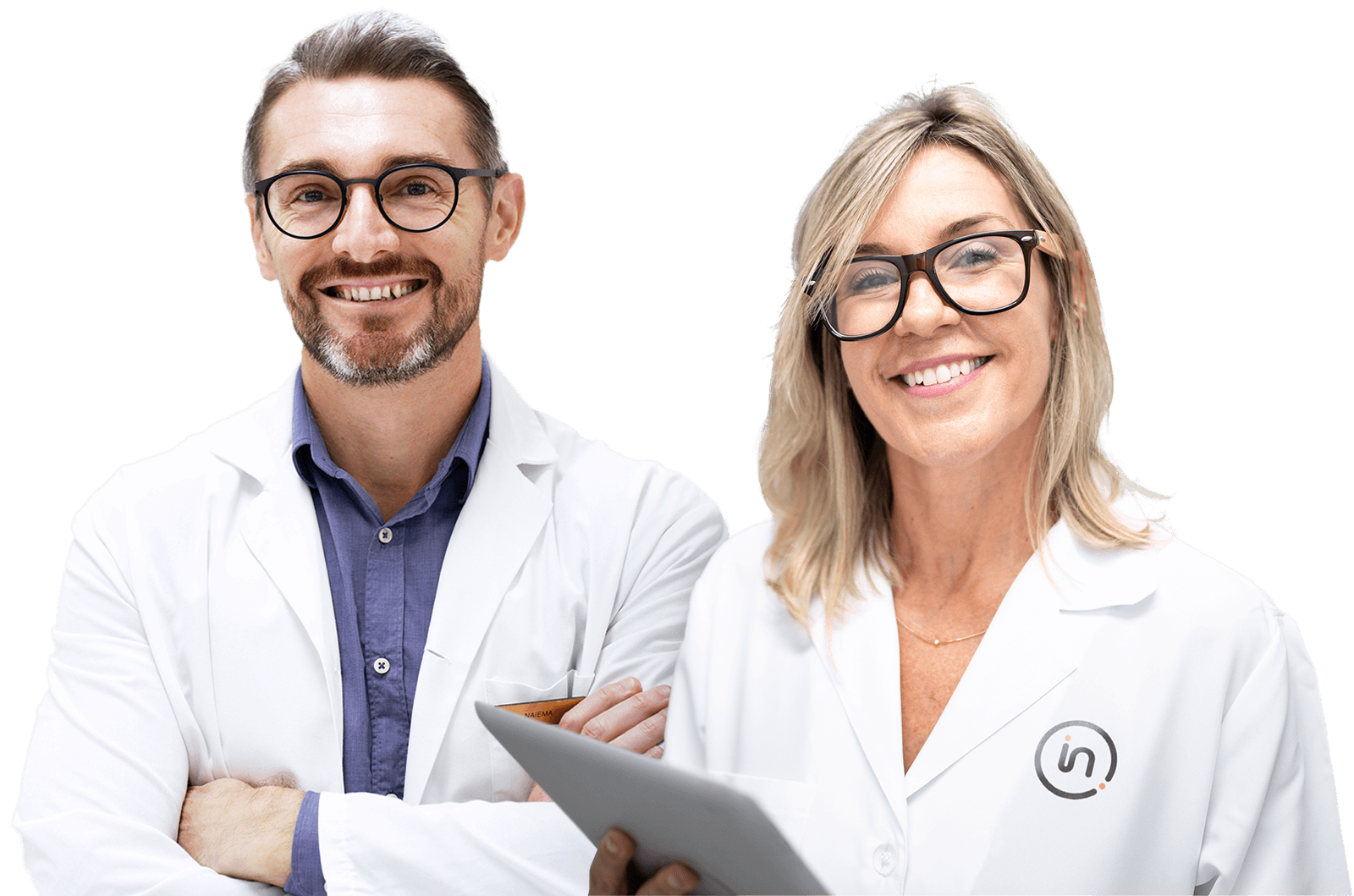