Ultrasonic remote sensors can improve data quality, offer the ability to operate remotely without human interaction and monitoring can be done online while eliminating operational downtime.
Non-destructive testing plays a critical role in processing, testing and structural evaluation of assets. Non-destructive testing (NDT) technologies including ultrasound, radiography, electro-magnetic and remote visual have evolved significantly over the past few years. Plant operators are increasingly looking at sensors to monitor the structural health of their equipment so that limited inspection personnel are required.
Ultrasonic remote sensors measure the wall (metal) thickness of the equipment to which they are attached, allowing measurement for the rate of corrosion of the equipment. This information can then be used by the client to determine the equipment's remaining useful life, or in other words, predict when the equipment may fail.
These sensors can also be connected as an array (many sensors in a grid pattern) on equipment and then either hardwired to a receiving station, transmitted via Wi-Fi, or linked to our AwareTM software so the data can be analyzed and trended. Such sensors are useful when inspectors face difficulty in gaining access to equipment (such that scaffolding or other access is required) and when the equipment has high rates of corrosion, requiring frequent inspector visits to monitor the equipment.
Optimal placement of sensors is key to gathering the most effective data. This requires personnel with experience of manual inspections of the same type of equipment. Intertek inspectors have the necessary experience and can install and monitor these sensors for our clients.
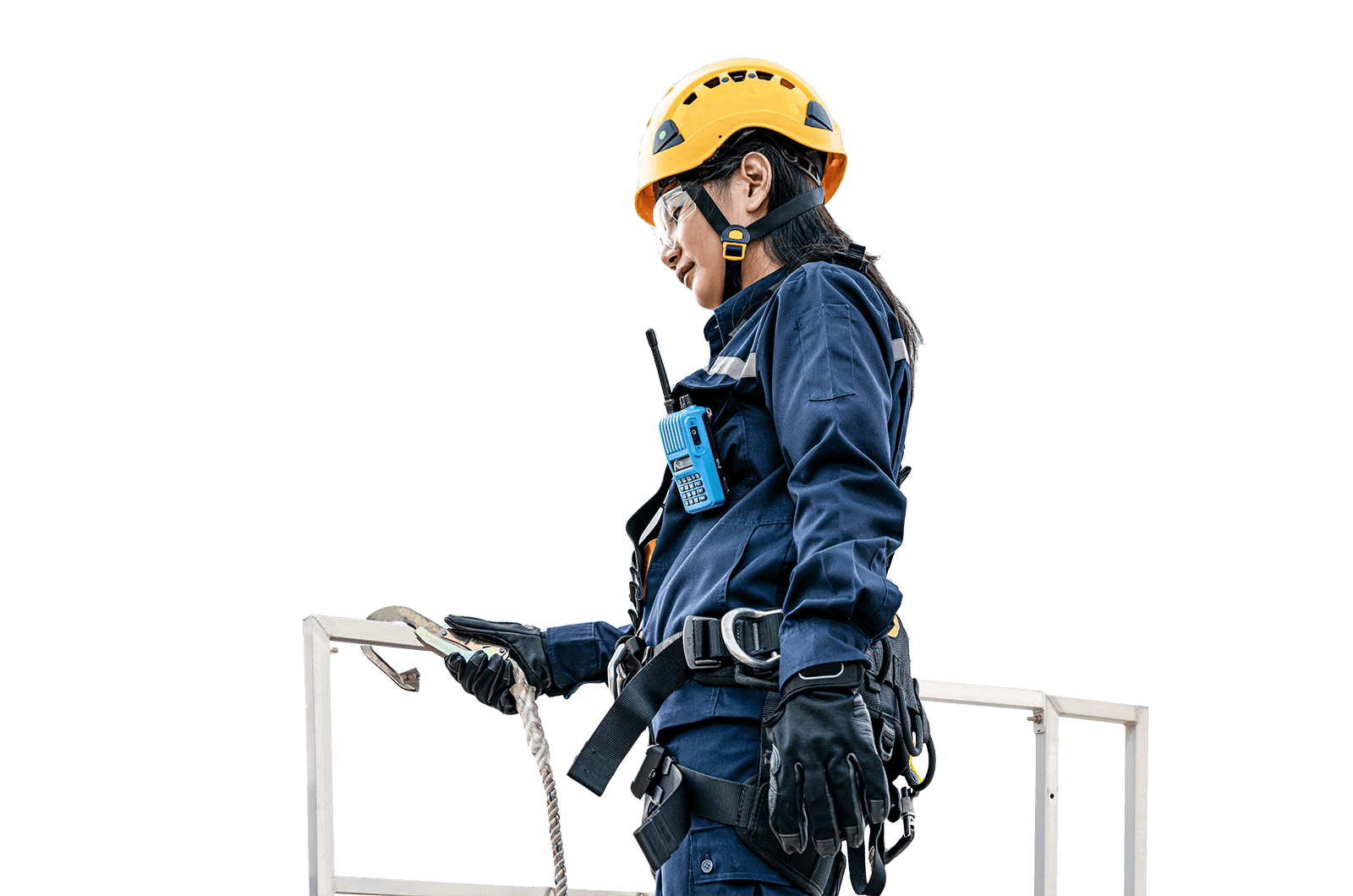