Adhesive testing to determine performance and properties across multiple industry applications such as aerospace, automotive, construction, packaging, industrial, medical and energy to support application development and quality assurance
Adhesive testing is necessary to evaluate the long-term reliability and durability of adhesive products in various applications. Advanced adhesives are now available for a wide range of industries, including building products, aerospace, automotive, and packaging. For each new requirement, substrate (e.g., foils, paper, textiles, metals, foam, plastic, rubber, or glass) or application, a customized adhesive product is likely required to meet the specific physical demands of the bonded joint and the stability requirements of the product in use. Adhesives can be difficult to evaluate due to their variety, chemistries, and curing processes. Accordingly, a multidisciplinary approach can be required, encompassing aspects such as the study of adhesive interfaces, assessment of mixing, categorization, and visualization of failure modes.
Relevant adhesive test methods and stringent testing procedures provide assurance against failure, which can occur due to incorrect resin or additive selection, inadequate amounts and curing, contamination issues, cross-contamination issues, substrate issues, or formulation issues. This testing also plays a key role in production quality assurance and helps troubleshoot quality issues.
Our experts produce swift and accurate performance adhesive test data for products used in various industries and applications, such as aerospace, automotive, and construction. The data we provide assists material engineers in the selection of materials in global markets. It includes adhesive strength testing such as tensile, shear, and peel data, as well as other adhesive property tests (e.g., impact, odor, and aging). Testing can be performed in hot/wet/dry conditions at ambient, elevated, or reduced temperatures. Additionally, we provide adhesion testing of coatings, chemical analysis and development support testing, quality assurance programs, and troubleshooting analysis investigations.
Adhesive Formulation Development Support:
Our adhesive formulation testing experts analyze adhesives across a wide range of applications, from packaging to transportation to the electronics industry. They have experience across a wide range of curing processes (heat-activated curing adhesives, UV-activated curing adhesives, anaerobic adhesives, moisture-activated, and pressure-sensitive adhesives) and chemistries (epoxies, urethanes, polyimides, acrylics, cyanoacrylates, silicones). We deliver both chemical testing and physical performance testing as tailored programs to meet your specific needs.
We support the development of new adhesive formulations through performance testing, including adhesion, peel, lap shear strength, shear modulus, tensile, flexural, impact, and cleavage strength, durability, fatigue, environmental resistance, conductivity, and mechanical properties (e.g., creep, fracture, and fatigue). We also analyze physical attributes (softening point, rheology, solids content, filler content, specific gravity, and color) and chemical analysis to gain in-depth understanding of the complex formulation components, their interactions, physical properties, long-term stability, relevant bonding, and aging processes, and an understanding of the processes that occur between the adhesive and the substrate interface. Techniques such as Differential Scanning Calorimetry (DSC) or Thermographic Analysis (TGA) are employed to study changes in physical properties that can occur during the curing process. We also perform accelerated aging tests and determine the rate of cure as part of the overall assessment to establish durability.
Adhesive Quality Assurance Programs:
We tailor quality assurance programs for your adhesive chemistries or curing processes to evaluate the critical attributes and fundamental properties of ongoing production batches, ensuring they meet specifications and supporting sourcing by monitoring the quality of incoming materials. Our QA programs typically include the collection of data to enable product and process performance, driving insight through the use of Statistical Process Control tools.
Troubleshooting Performance or Quality Issues:
To solve adhesive quality issues, we apply a wide range of spectroscopy (FTIR, RAMAN, RAMAN microscopy), microscopy (optical, scanning electron microscopy), chromatography (GC-MS, HS-GC), and mass spectrometry alongside key performance tests such as lap shear or peel. These techniques are strategically applied to address issues such as integrity, mixing, consistency, and to ensure more control over a wide variety of potential future issues. Mass spectrometry (either MALDI-TOF or LC-MS) may be employed to yield information about the buildup of oligomers during curing. This can include bulk oligomers and the formation of low levels of adducts during mixing. We may also use techniques such as Differential Scanning Calorimetry (DSC) or Thermographic Analysis (TGA) to study changes in physical properties that can occur during the curing process.
Adhesives Strength Testing:
- Adhesive Peel Test or Stripping Strength of Adhesive Bonds (180 degree peel) ASTM D903
- Bond Strength / Ply Adhesion ASTM F904
- Climbing Drum Peel of Adhesives ASTM D1781
- Peel Adhesion ASTM D3330
- Peel Adhesion to Rigid Substrates ASTM D429
- T-Peel of Adhesives ASTM D1876
- Floating Roller Peel of Adhesives ASTM D3167
- Lap Shear Metals ASTM D1002
- Lap Shear Adhesively Bonded Plastics ASTM D3163
- Lap Shear Sandwich Joints ASTM D3164
- Lap Shear Adhesive Joints ASTM D3528
- Lap Shear Thick Adherend Metal ASTM D5656
- Lap Shear Adhesion for Fiber Reinforced Plastics ASTM D5868
- Tensile Adhesion Properties ASTM D1623
- Tensile Strength of Sandwich Constructions (Flatwise Tensile) ASTM C297
Additional Adhesive Tests:
- Exposure of Adhesives to Artificial Light (QUV) ASTM D904
- Determination of Odor of Adhesives ASTM D4339
- Moisture Conditioning ASTM D5229
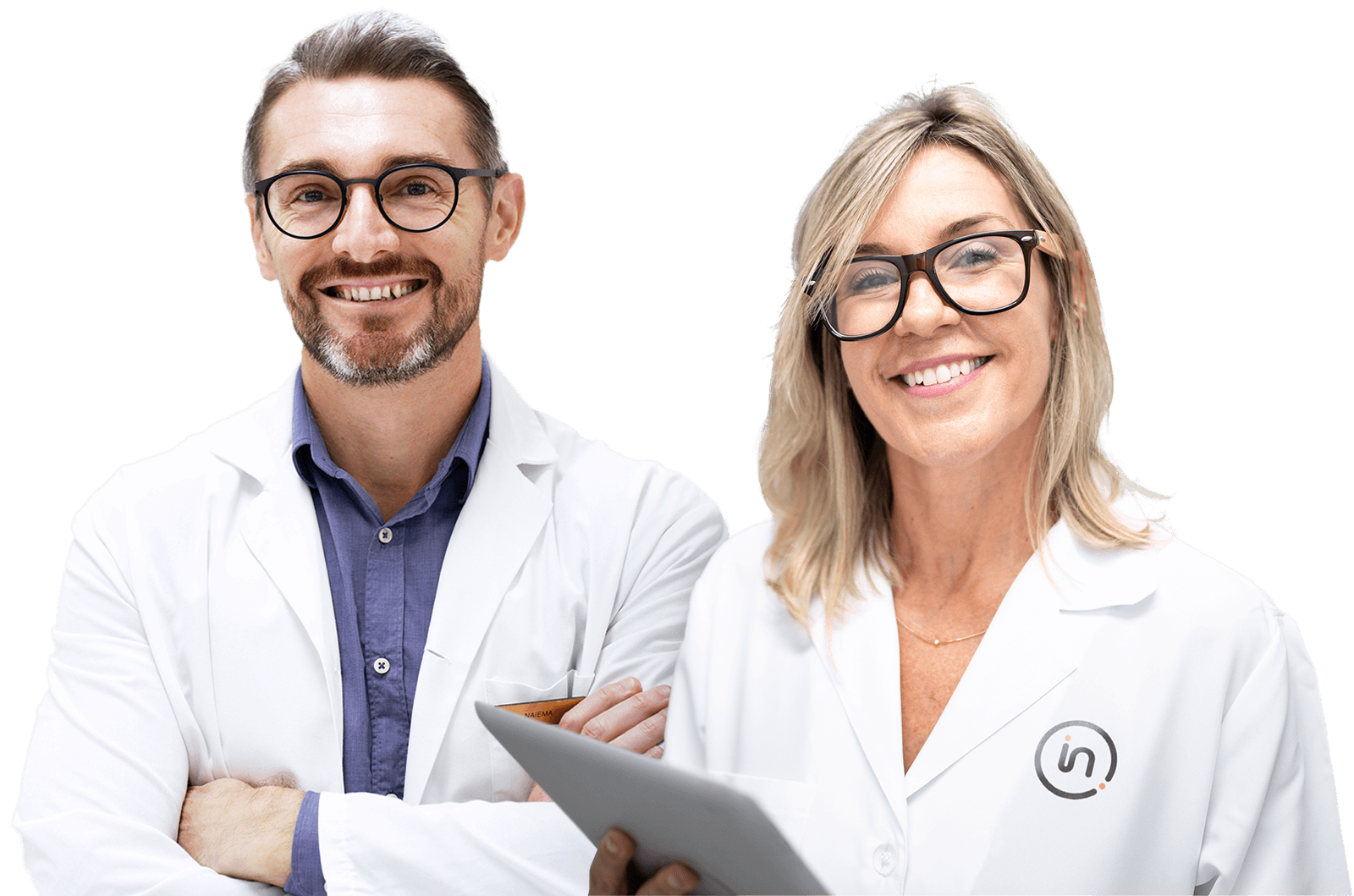