Our polymer compounding services include plastic compounding using lab-scale single or double-screw compounding, moulding and extrusion expertise followed by polymer testing, such as mechanical or rheological parameters.
Polymer compounding is the process of mixing or blending polymers and additives to achieve a homogeneous blend and is a step in the polymer development process. Execution of compounding on lab scale, instead of using industrial-scale plastic compounding lines, is beneficial for supporting test trials. Intertek's lab scale polymer compounding services supports companies in development processes of new compound recipes.
The need for lightweight, more durable, recycled polymers and low-emission materials, coupled with the increasing focus on using recycled materials, is forcing the polymer and plastics industry to continuously develop new, advanced materials; polymer compounding test trials play a key role in this innovation process. The goal is to improve or tailor properties such as physical, optical, aesthetic or thermal characteristics of the base material in relation to the intended application. Other areas of interest are the reduction or control of emission of volatiles, leaching or migration of substances.
Polymer Compounding Services
Our polymer experts run compounding trials within our modern polymer pilot plant facilities. In addition to single-screw compounding, Intertek also provide double-screw compounding, enabling the industry to test and evaluate materials on a small scale.
For the support of a standard material R&D evaluation, approximately 3-5 kg compound is required for physical and analytical material characterisation/evaluation. In the compounding process a range of substances are being used for optimization such as carbon fibres, anti-oxidants, colourants, wood fibres, cellulose fibres, flame retardants, talcum or glass. These additives can be added as masterbatch or powder to the base polymer material.
Our customers will receive the benefits of a Coperion ZSK 18 MEGAlab twin-screw, co-rotating laboratory extruder Ø 18 mm, L/D 44. This unit has a modular construction with exchangeable barrels and all standard screw elements. Our additional polymer processing services include polymer trial injection moulding, blown film and cast film extrusion.
Our twin-screw plastic compounding equipment includes:
- 2 loss-in-weight feeders
- 1 twin screw side feeder
- 2 atmospheric degassing valves
- 1 vacuum system
- Die plate 2x diameter 3 mm
- Pelletizer
- Measuring P and T
- Operating window: Max. Temperature 400°C, Throughput 200 gram - 40 kg/h
Decades of Polymer Development Support
Our laboratories have decades of expertise in polymer and plastic product development. Our expertise includes troubleshooting, process optimisation, formulation, physical, mechanical and thermal testing, chemical analysis, regulatory compliance and certification.
Intertek technical polymer experts will discuss your requirements and assist you with a basic or thorough evaluation of your polymer compounds and materials. Contact our specialist staff to discover how our state-of-the-art facilities may assist your company’s R&D, colourant, additive, minerals, raw materials, masterbatch and testing requirements.
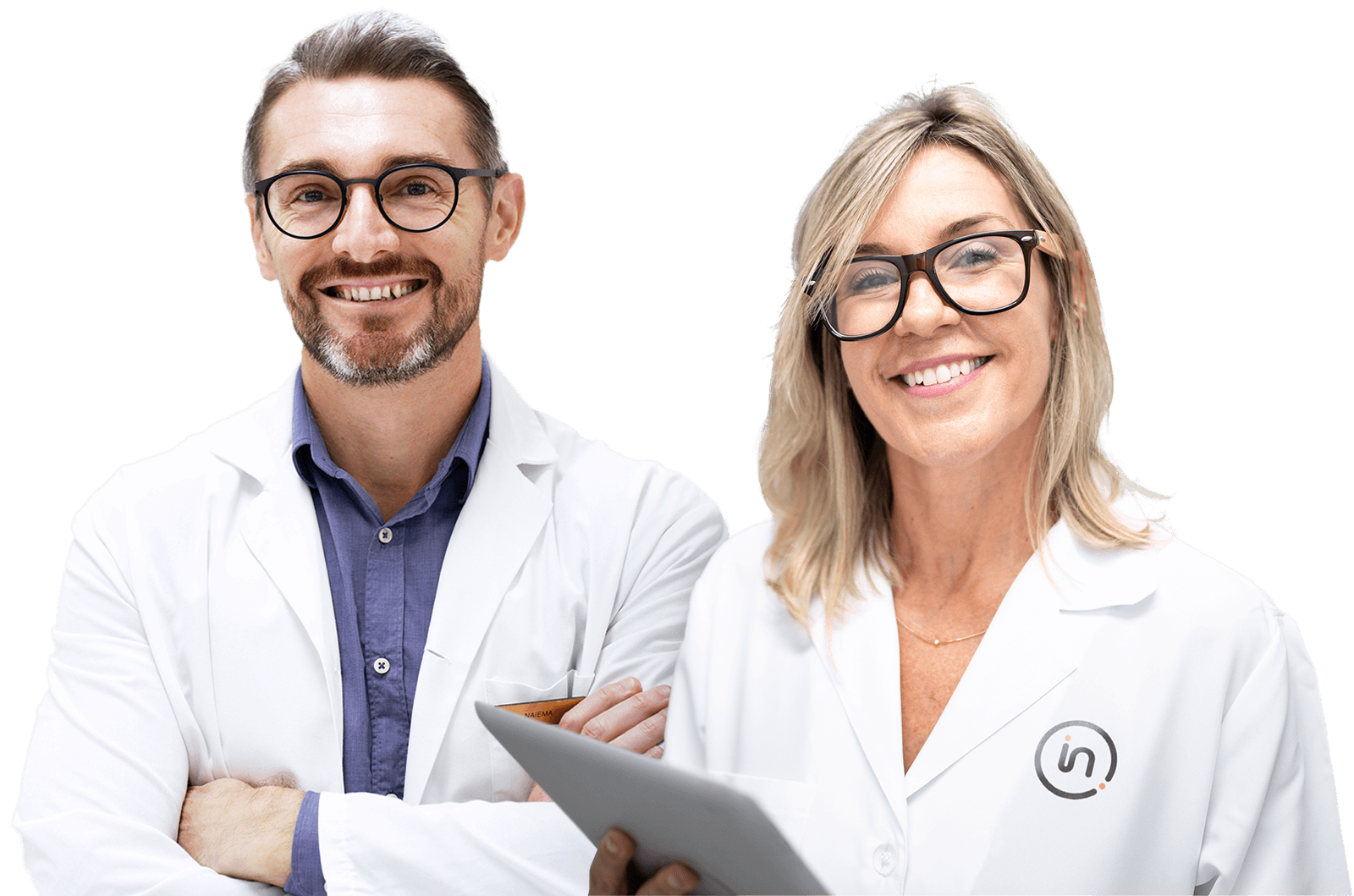