Rheology laboratory testing of polymers to determine the rheological (flow) properties of materials, gels and pastes, to optimise processing and properties
Polymer rheology testing is the study of how the stress in a material or force applied is related to deformation and flow of the material. Understanding the rheological properties of polymers through laboratory testing can help to optimize products and process conditions, thereby saving costs and minimizing potential waste.
Our polymer science experts perform rheological property testing on a wide range of polymers such as polyolefins, liquids, adhesives, gels and pastes using a wide range of temperatures and deformation rates (both shear and extensional). Rheology tests are performed while the polymer is in the melt phase or while the polymer has been dissolved in a solvent for intrinsic viscosity and relative viscosity.
We can apply our rheology test capabilities in diagnostics, design or optimisation problems, using quantitative polymer rheology measurements to help you to optimise processing with minimal product degradation, or to optimise molding parameters which can lead to greater cost efficiencies costs and enhanced production rates.
The rheology data we generate and the insight we can bring to your development process can help ensure that the polymer’s properties meet specifications for the end use (texture, product pour) and product quality: surface distortions, anisotropy, strength, structure development.
- Rotational Rheology Laboratory Stress and strain rate control options are available in air or an inert atmosphere suitable for polymer melts, viscous fluids, dispersions, emulsions and other materials, from ambient temperatures up to 400°C
- Capillary Rheometry Providing data for design packages. Thermal stability, onset of unstable flow, and wall slip measurements. Measurement of transient extensional properties as a tool to predict/troubleshoot polymer flow behaviour in many common forming processes such as extrusion, blow moulding and injection moulding.
- Melt Flow Rate and Melt Flow Index (ASTM D1238, ASTM D3364, ISO 1133)
- Dilute Solution Viscosity Measurements (ASTM D1243, ASTM 2857, ASTM D4603, ISO 489)
Our polymer scientists collectively possess many years’ experience in the characterisation of these challenging materials. Our rheology labs are located in Europe and North America, and we routinely work with some of the most innovative organisations from around the world. Discover more on our Polymer Rheology Testing in our On Demand Webinar.
Working across diverse industries such as automotive, aerospace, medical devices, industrial production and stakeholders in the polymer supply chain we deliver a detailed understanding of rheological properties through laboratory testing, helping you to optimize products and process conditions.
Rheology services:
The ultimate goal is to modify the structure of the polymers in such a way that the process ability of these materials increase without sacrificing the properties of the end product (tensile strength, impact resistance, hardness and so on). Rheology is the desired technique due to its sensitivity to changes in the structure of polymers. This paper describes a number of rheological testing techniques available at Intertek. Three different types of polyethylene, HDPE, LDPE and LLDPE, were studied applying these rheological testing techniques.
Capillary Rheology Video
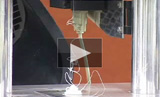
View this video about capillary rheology.
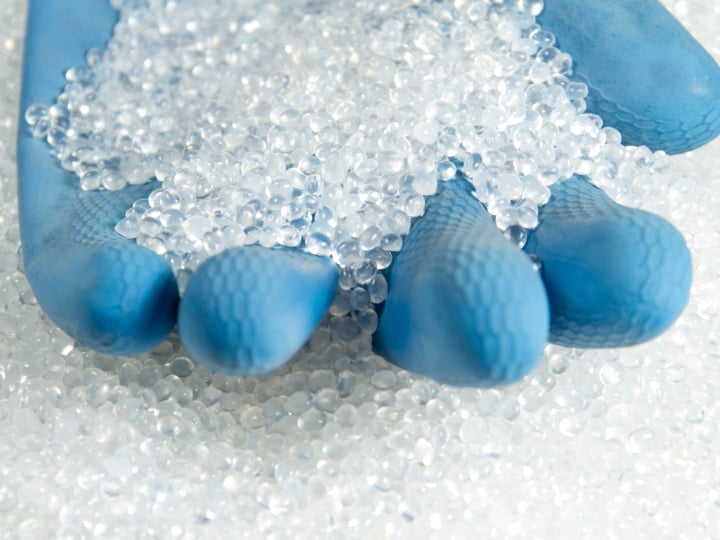
Polymers and Plastics
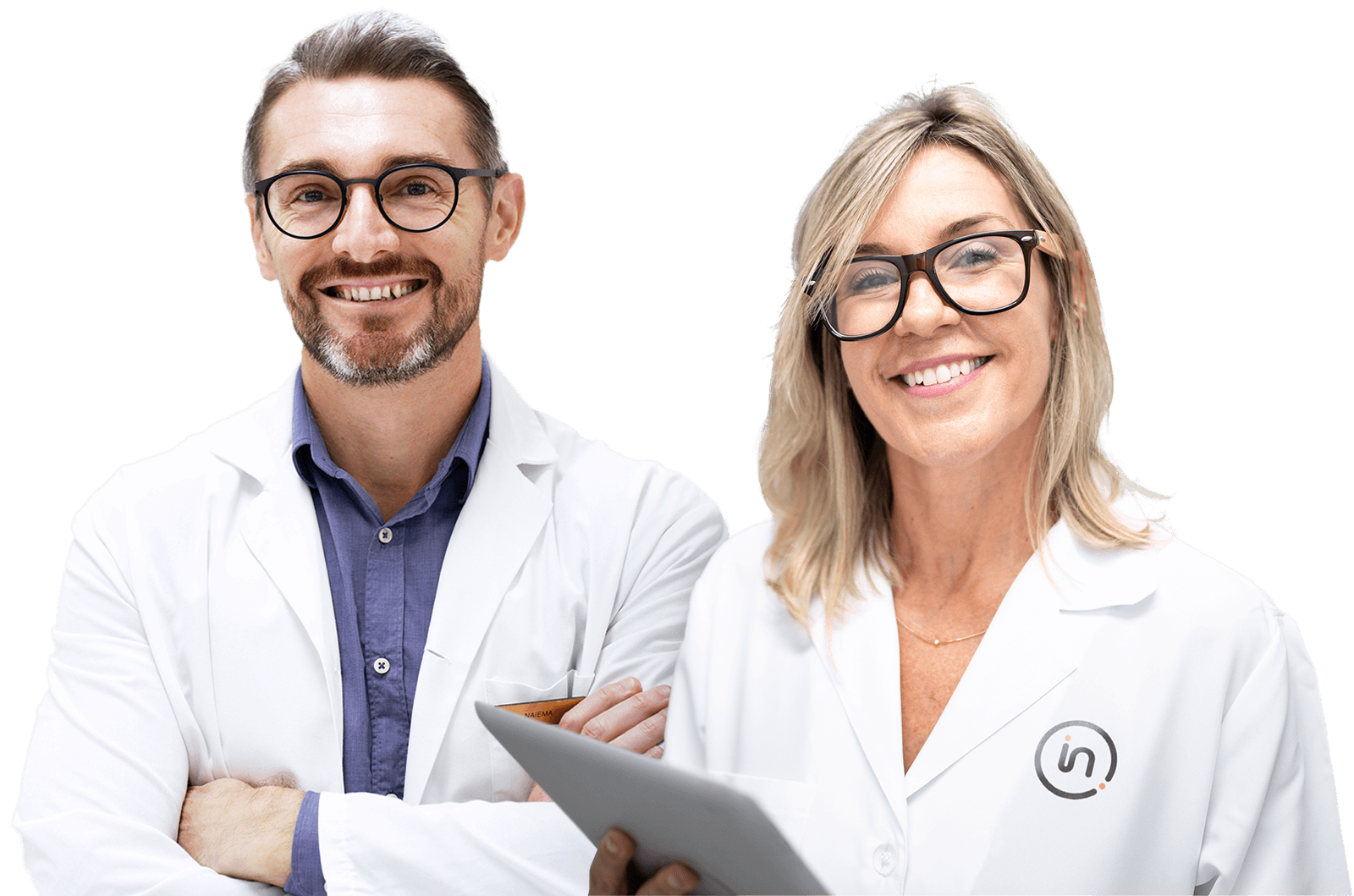