Effective April 30, 2015
Standard Information
Addendum SUN: Standard again revised March 20, 2014 and those new/revised requirements added to this existing SUN from previous revisions of January 10, 2012 and May 17, 2010. Effective Date pushed out to April 30, 2015 to accommodate.
Standard Name: Standard for Industrial Trucks, Internal, Combustion Engine-Powered
Standard Number: UL 558
Standard Edition and Issue Date: 10th Edition, January 10, 2012
Date of Revisions: January 10, 2012 and March 20, 2014
Date of Previous Revisions to Standard: May 17, 2010
SSQ Category: Q2
Effective Date of New/Revised Requirements |
Effective Date: April 30, 2015
Overview and Description of Changes
Standard Info: Standard for Industrial Trucks, Internal, Combustion Engine-Powered , UL 558, 10th Edition, January 10, 2012
Impact Statement: A review of all Listing Reports is necessary to determine which products comply with the new/revised requirements and which products will require re-evaluation and test. NOTE: Effective immediately, this revised standard will be exclusively used for evaluation of new products unless the Applicant requests in writing that current requirements be used along with their understanding that their listings will be withdrawn on the Effective Date of January 10, 2015,April 30, 2015. unless product is found to comply with the new/revised requirements.requirements (this effective date is based on the Effective Date given for clauses 11.1.3, 11.2.1, 11.2.2, 27.3, 31.4.1, and 31.4.2).
New/revised paragraphs covering Electric Fuel Pump Wiring, Vibration Test for Fuel Filters, Removal of Metallic tube fitting vibration test, Explosion and Hydrostatic Strength Test for Electric Fuel Pumps, and Nonmetallic fuel tank requirements for cleaning equipment in Supplement SB. See top of attached Construction Evaluation form for details.
Overview: Removal of “New and Unusual” scope paragraph
Revision of requirements for battery leads
Revisions to exhaust system requirements
Revisions to fuel system requirements
Enclosing electrical components for “S” Type trucks
Changeover switch – Dual Fuel
Sample & Information Required: The following types of equipment must be submitted for re-evaluation of the characteristics noted:
- LP Gas fuel system components must be evaluated to the revised clauses of Section 11.
- Parts subject to the vibration test must be re-tested using the test method described in section 31.4
- Battery leads must comply with Outline for Battery Leads
- Exhaust systems on all trucks must be reevaluated for compliance with revised standard
- S-type trucks must have their electrical system evaluated for compliance with revised requirements
- Dual fuel units employing changeover switch
NOTE: A Previous SUN was issued for 9th edition of the standard with revisions dated 05/17/2012. In that SUN notice, paragraphs 5.1.1, 5.1.2, 5.1.3 and 5.4 were given an Effective Date of 05/17/2013. Note that those clauses are now re-numbered as 8.1, 8.2, 8.3 and 8.5, but the requirements remain the same, as does the effective date for those clauses.
Description of New/Revised Technical Requirements
Clause | Verdict | Comment | NC# |
SUN UPDATE REVIEW | |||
|
|
|
|
|
| New/Revised Requirements from Revisions March 20, 2014 |
|
27.6 | Info | Revised to refer to Section 8: Electrical connections shall be threaded terminal posts, spade type, or integral insulated lead wire, as constructed per Section 8. |
|
31.3.1 |
| Revised to clarify only fuel filters outside: A fuel filter located outside of the fuel tank shall not become loosened from its mounting or be otherwise damaged from its normal mounting position under the conditions described in 31.4.1. |
|
35.6 | Info | Added: In the event that the fuel pump construction is such that an explosion does not occur when tested in accordance with 35.1 – 35.5, the fuel pump shall be considered acceptable. |
|
f36.1 | Info | Added Exception: A fuel pump that complies with 35.6 is not required to comply with the Hydrostatic-Strength Test. |
|
SB2.2 |
| Added requirement for non-metallic fuel tanks: A nonmetallic fuel tank shall comply with the requirements in Sections 10.3 and SB7. |
|
SB7.1 |
| Added test requirement: Internal pressure resistance test |
|
SB7.2 |
| Added test requirement: Impact test |
|
|
|
|
|
|
| TYPES G, D, and LP |
|
8.1 |
| (e) Battery Leads must comply with the Outline for Battery Leads, UL Subject 2726. |
|
9.1 |
| The exhaust system beyond the manifold shall be supported at least 3 inches (76.2 mm) clear of flammable materials, excluding flexible mountings, and at least 2 inches (50.8 mm) clear of fuel- and electrical-system parts and shall not subject to drippage of fuel, oil, or grease. See also Temperature Tests, Section 23. |
|
9.2 |
| The exhaust system shall conform with the test requirements of the Exhaust System Test, Section 25 |
|
9.3 |
| A muffler and/or catalytic converter shall be provided on each truck |
|
11 | G | Fuel Systems – LP Gas |
|
11.1.3 |
| Each applicable LP-Gas component, excluding fuel lines, hoses, and tanks, shall comply with the requirements in the Outline for LP-Gas Automotive Accessories, Subject 1337. |
|
11.2.1 |
| When a vehicle incorporates a non-removable ASME fuel container, the container shall have a maximum allowable working pressure (MAWP) of 312 psig (2.15 MPa). It shall be marked with the ASME ²U² symbol and the design working pressure. |
|
11.2.2 |
| When a vehicle incorporates a non-removable DOT fuel container, the container shall be constructed, tested, and marked for a minimum service pressure of 240 psig (1.7 MPa). It shall bear the marking DOT-4B240, DOT-4BA240, DOT-4BW240, or DOT-4E240. A DOT fuel container assembly shall comply with the requirements in the Outline of Investigation for LP-Gas Cylinder Assemblies, Subject 2003. |
|
|
|
|
|
|
| Types GS, DS, and LPS |
|
13.1 |
| The electrical system shall comply with 8.1 – 8.8 and 13.2 – 13.9. |
|
13.2 |
| Wiring terminals shall be protected by insulating boots or covers, unless they are intentionally connected to ground on the truck frame when the truck is in operating condition. |
|
13.3 |
| Individual insulating boots shall be tight-fitting, completely enclose the terminal, and be acceptable for the temperatures to which they are exposed. |
|
13.4 |
| Reusable type boots shall be provided on other than crimped, soldered, or riveted terminals. |
|
13.5 |
| Covers employed in lieu of insulating boots shall be of metal or equivalent material. Among the factors taken into consideration are: |
|
13.6 |
| Spacings between positive terminals and metallic enclosures employed in lieu of boots shall be a minimum of 1/2 inch (12.7 mm) or be separated by a nonconductive material not less than 1/32 inch (0.8 mm) thick that cannot be removed during normal operation or servicing. |
|
13.7 |
| Those portions of a component such as an alternator, motor, switch, relay, etc., which emit sparks shall be totally enclosed. |
|
13.8 |
| When a nonmetallic enclosure is used to comply with 13.7, the enclosure shall comply with the following requirements in the Standard for Polymeric Materials – Use in Electrical Equipment Evaluations, UL 746C, Path II: |
|
13.9 |
| A manual-disconnect switch readily accessible to the operator when in his normal operating position shall be installed in the battery and charging circuits to permit quick disconnect in case of an electrical disturbance. |
|
14.1 |
| The exhaust system shall comply with 14.2 – 14.5 in addition to Exhaust Systems, Section 9. |
|
14.2 |
| The exhaust piping shall be formed of material having strength, rigidity, and resistance to corrosion equivalent to mild-steel tubing having a minimum thickness of 0.053 inch (1.3 mm). When exhaust piping is of multi-wall construction, one wall shall be formed of a solid metallic construction. |
|
14.3 |
| The muffler or catalytic converter shall be of welded or crimped seam steel construction, using single or multi-wall material having a minimum thickness of 0.053 inch (1.3 mm). |
|
14.4 |
| An aspirator shall be of metal and have a backfire deflector securely connected to the fresh-air intake. The backfire deflector shall prevent the passage of flame during backfire conditions and shall be so located that, in the event its fastening means loosens, it shall remain securely connected to the air intake system. |
|
14.5 |
| The exhaust system shall conform with the test requirements of the Exhaust System Test, Section |
|
|
|
|
|
|
| Types G/LP and GS/LPS |
|
17.4.1 |
| A fuel changeover means shall be provided that prevents operation of both fuels at one time except for the fuel remaining in the common fuel system components at the time of changeover. |
|
17.4.2 |
| The changeover control shall provide a three-way selector means or device providing individual selection of each of the fuels plus a position where both fuels are shut off. Each position shall be permanently marked with its function. |
|
17.4.3 |
| The changeover control shall be located so that it is readily accessible to the operator. |
|
17.4.4 |
| A permanent marking place located on or adjacent to the changeover control shall be provided with the following statement: |
|
17.5.1 |
| A fuel changeover means shall be provided that prevents operation of both fuels at one time except for the fuel remaining in the common fuel system components at the time of changeover. |
|
17.5.2 |
| The changeover control shall provide a three-way selector means or device providing individual selection of each of the fuels, plus a position where both fuels are shut off. Each position shall be permanently marked with its function. |
|
17.5.3 |
| The changeover control shall be located so that it is readily accessible to the operator. |
|
17.6.1 |
| A fuel changeover means shall be provided that prevents operation of both fuels at one time. |
|
17.6.2 |
| The changeover control shall provide a two-way selector means or device providing individual selection of each of the fuels. Each position shall be permanently marked with its function. |
|
17.6.3 |
| If the changeover control is located outside of the engine compartment and is located within an low voltage and limited power circuit, the tests in Section 30, Changeover Switch - Dual Fuel, are not applicable. |
|
|
|
|
|
|
| Type DY |
|
19.1 |
| The exhaust system shall comply with Exhaust Systems, Section 14 and with 19.2 and 19.3. |
|
19.2 |
| The exhaust system shall also comply with the temperature limitations specified in Temperature Limitations, Section 21. |
|
19.3 |
| Gaskets employed in the exhaust system shall be of metal construction. Asbestos gaskets with a metal exterior covering are also acceptable. |
|
|
|
|
|
|
| PERFORMANCE – ALL TYPES |
|
25.1 |
| Exhaust system tests – General |
|
25.2 |
| Exhaust system tests, types G, LP, GLP |
|
25.3 |
| Exhaust system tests, types GS, DS, LPS, GS/LPS, and DY |
|
27.3 |
| When the case or other external components, of a fuel pump located outside of the fuel tank, are non-metallic, tests described in 10.3 and the following requirements in the Standard for Polymeric Materials For Use in Electrical Equipment Evaluations, UL 746C, under Path II shall be conducted: |
|
30 | G | Changeover switch –dual fuel |
|
30.1 |
| Terminals and terminal construction shall be of such size and shape as to provide the necessary capacity and mechanical support for the conductors connected to them. Terminals employing a threaded screw or bolt for securing the conducting lug to a terminal plate shall provide a minimum of two full threads |
|
30.2 |
| The assembly shall be capable of resisting the effects of vibration. See 31.2.1. |
|
30.3 |
| The enclosure shall be of metal, molded-phenolic composition, or equivalent material evaluated in accordance with 30.4. |
|
30.4 |
| Among the factors which are to be taken into consideration when judging the equivalency of a nonmetallic enclosure are: |
|
30.5 |
| The switch assembly shall function as intended and the contacts shall not weld together or show excessive pitting when operated for 6000 cycles at the electrical load it is intended to control. |
|
30.6 |
| The assembly shall comply with the Dielectric Voltage-Withstand Test, Section 33. |
|
30.7 |
| Spacings through air and over surfaces between uninsulated live parts of opposite polarity, and between uninsulated live parts and dead metal parts that are likely to become energized shall be a minimum of 3/64 inch (1.2 mm). |
|
31.4.1 |
| Vibration test method: The sample shall be subjected to variable frequency vibration along each of three axes (horizontal, lateral, and vertical) for 8 hours in each plane (24 hours total) at a peak-to-peak amplitude of 0.040 ±0.001 inches (1.3 ±0.00004 mm). The frequency of vibration is to be continuously varied, at a uniform rate, from 10 to 60 to 10 hertz every 4 minutes. |
|
41.4.2 |
| For this test, peak-to-peak amplitude is defined as the maximum displacement of sinusoidal motion (total table displacement). |
|
END OF SUN REVIEW EVALUATION |
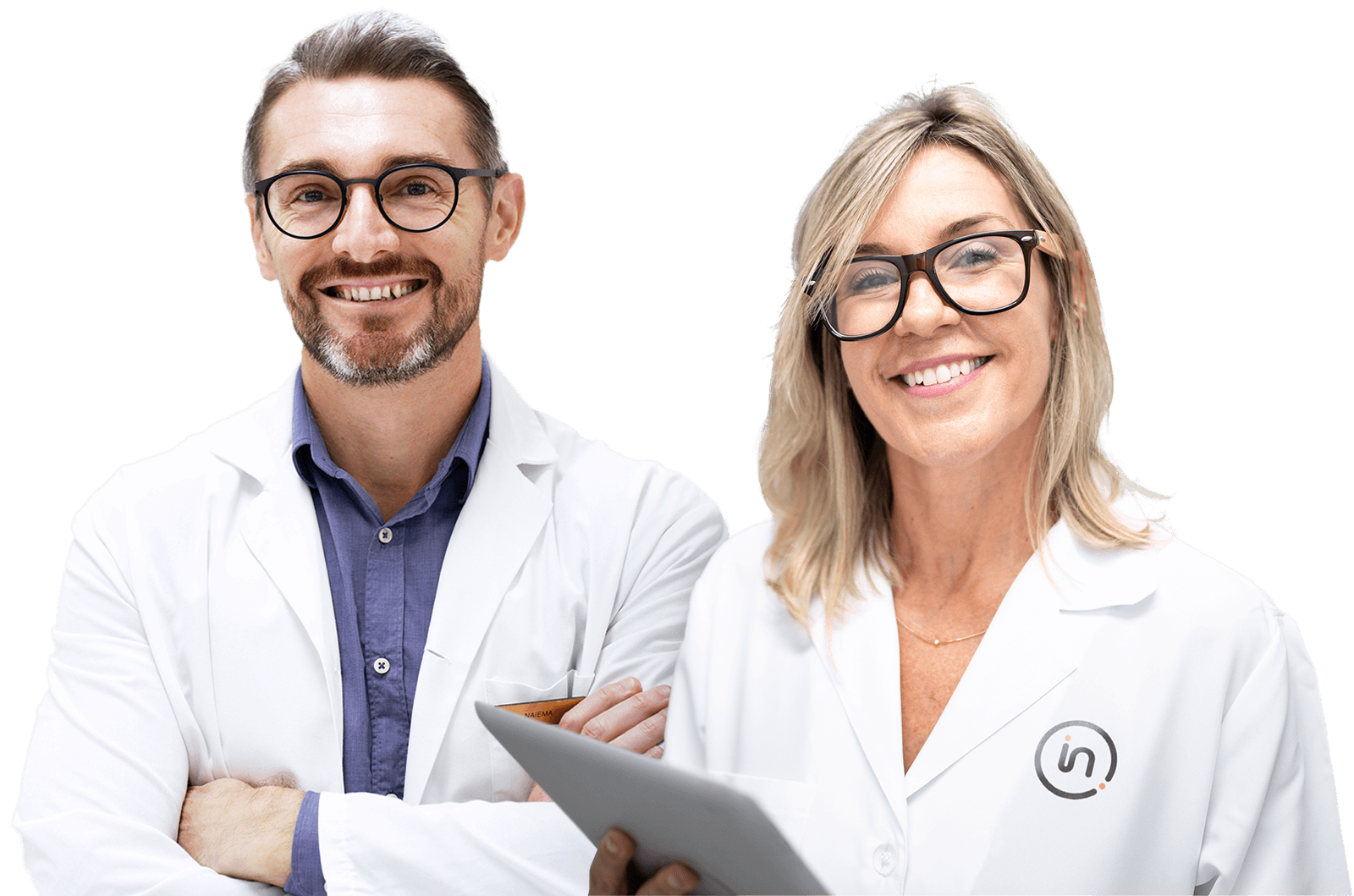